China’s economy continues to grow, and specialized, differentiated manufacturing advances. Precision aluminum alloy products have gained popularity across major industries, with rising demand in sectors like automobiles, high-speed locomotives, and communications.
Aluminum alloy is becoming a key structural material, driving rapid growth in the precision aluminum alloy manufacturing.
More CNC machining companies are fueling this growth through technological innovation and equipment upgrades.
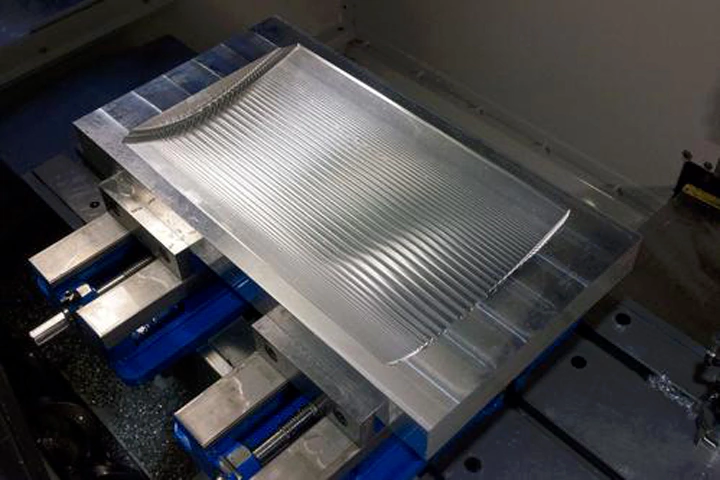
Customized Aluminum Alloy Parts Market
As precision machining technology improves, CNC (Computer Numerical Control) machining centers have become the main method for customizing aluminum alloy parts.
These centers control the machining process accurately, improve efficiency, reduce errors, and meet the needs of complex parts.
Precision aluminum alloy parts are used widely in automotive, aviation, electronics, communications, and medical industries due to their excellent mechanical properties and lightweight characteristics.
For example, in the automotive sector, aluminum alloy is increasingly used in body parts and power systems as the trend toward lightweight grows.
This reduces fuel consumption, boosts fuel efficiency, and extends vehicle lifespans. Aluminum alloy is the best lightweight material and plays a crucial role in modern car manufacturing.
Additionally, the rise of new energy vehicles and stricter fuel consumption regulations further promote aluminum’s use in the automotive industry.
Precision Aluminum Alloy Machining
Shenzhen Ruiyi Precision Machining Factory has long specialized in CNC machining of various hardware parts, including aluminum, copper, stainless steel, and more.
Their products cover industries such as metal casings, hardware products, metal panels, environmental equipment, non-standard miniature parts, copper/aluminum alloys, medical equipment, instruments, precision machinery, communications, electronics, and automotive.
Ruiyi Precision is committed to delivering high-quality products with advanced technology and strict quality control.
Ruiyi Precision understands that in a competitive market, technology and equipment drive business growth.
Like a tree, the enterprise forms the root, while technology and equipment are the branches and leaves.
Despite industry challenges and market uncertainty, innovation in technology and ongoing equipment upgrades enable the company to grow and seize new opportunities.
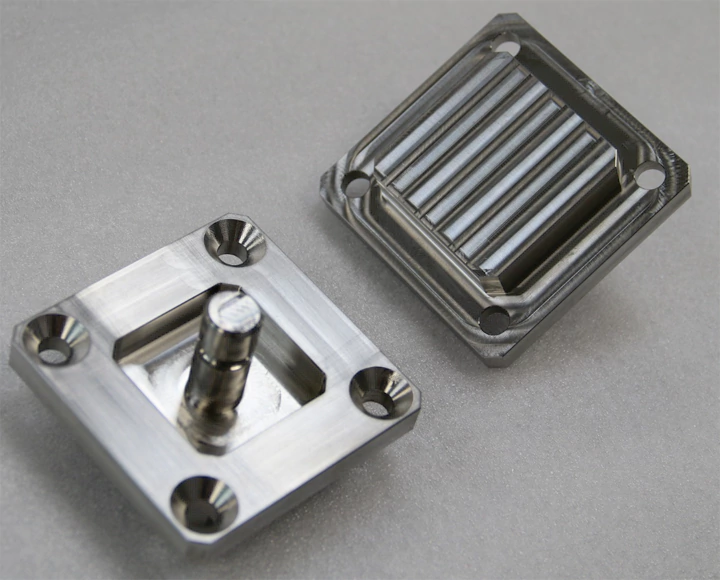
Industry Trends and Future Development
The rapid growth of the automotive, communications, aviation, and electromechanical sectors has increased demand for precision aluminum alloy parts.
As a result, the CNC machining industry is moving toward high-value-added, high-tech products.
CNC machining companies must continuously enhance their technology and upgrade their equipment to meet market demands for high-precision, complex parts.
The aluminum alloy CNC machining industry faces enormous development opportunities.
With advanced technology and equipment, companies can capitalize on explosive growth and make breakthroughs in the industry.
The demand for aluminum alloys, especially in new energy vehicles and lightweight materials, will experience unprecedented growth.
Supporting Industry Development
To adapt to market demand and enhance competitiveness, Ruiyi Precision focuses on technical R&D, optimizes processing technology, and upgrades equipment.
The company also promotes products through internet platforms to expand its market share in CNC aluminum alloy part machining.
Whether in traditional car manufacturing or new energy vehicles, Ruiyi Precision provides customized aluminum alloy machining services that meet complex processing needs.
If you want to learn more about CNC machining of aluminum alloy prototypes or need custom machining services, feel free to contact us. We offer professional technical support and high-quality products.
Contact Information:
Email:prototype@ruiyi-cncmachining.com
FAQ:
Aluminum alloy is lightweight, strong, corrosion-resistant, and easy to machine. These properties make it ideal for industries such as automotive, aviation, electronics, and communications that demand high performance and reduced weight.
CNC (Computer Numerical Control) machining provides precise, automated control over the manufacturing process. It allows for high-accuracy production of complex, customized aluminum alloy parts while improving efficiency and minimizing errors.
Precision aluminum alloy parts are widely used in:
Automotive (e.g., body and power system components)
Aerospace and aviation
Medical devices
Electronics and communications
Industrial equipment
Aluminum alloys help reduce vehicle weight, which lowers fuel consumption and increases efficiency. This is especially critical for NEVs, where lightweight construction directly enhances battery performance and driving range.
Ruiyi specializes in CNC machining of aluminum, copper, stainless steel, and more. They combine advanced equipment, strict quality control, and technical innovation to deliver high-quality parts across multiple industries.
The industry is shifting toward high-value-added and high-tech production, focusing on improved precision, complex geometry, and smaller tolerances. Companies must upgrade equipment and continuously innovate to stay competitive.
Challenges include market competition, technological demands, and material cost fluctuations. However, the growth of industries like automotive, NEVs, and electronics offers significant opportunities for CNC firms equipped with advanced technology.
Aluminum alloys reduce vehicle weight without compromising strength. This improves fuel economy, extends vehicle lifespan, and meets regulatory standards for emissions and efficiency.
Ruiyi focuses on:
Technical R&D
Continuous equipment upgrades
Optimizing machining processes
Expanding market reach through digital platforms
You can contact Ruiyi Precision Machining Factory for professional consultation and high-quality custom CNC machining services. They provide full support for prototyping and production based on your design and application requirements.