This article introduces the development and advantages of advanced CNC machining technology, including machining equipment and cutting tools, and analyzes key aspects of the machining process.
High-Speed CNC Machining Technology
High-Speed Machining
This advanced manufacturing technology offers more than just speed—it improves efficiency, enhances quality, and reduces material consumption, making it essential in modern industry.
It includes turning, milling, and drilling at elevated speeds.
This technology boosts efficiency, reduces cutting forces, improves quality, simplifies processes, and lowers energy use—widely used in high-end equipment machining.
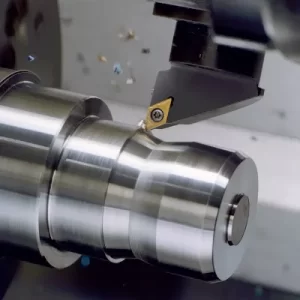
High-Speed CNC Machining Equipment
Advanced CNC equipment surpasses standard machines in dynamic performance, thermal stability, and overall efficiency.
The CNC and servo systems, machining status monitoring systems, electric spindles, and cutting tools all require higher technical standards and specifications.
High-Speed Cutting Tools
Cutting tool technology is crucial for ensuring machining quality.
Proper high-speed cutting tool structures, materials, and monitoring technology are essential for increasing cutting speed, material removal rates, machining precision, and quality.
High-speed cutting tools differ from traditional ones by reducing stress, boosting rigidity, improving connections, and enhancing high-temperature performance.
Tool materials must have excellent mechanical properties, thermal stability, impact resistance, and wear resistance, with common materials including super hard alloys, ceramics, and carbides.
High-Speed Machining Processes
High-Speed Machining Process Technology
Advanced machining process technology includes planning process routes, selecting tools, determining cutting methods, and optimizing cutting parameters.
When machining different materials, it is crucial to reasonably select cutting methods, tools, paths, and cooling methods.
These techniques must integrate tool materials and parameters for optimal performance.
High-Speed Machining Process Optimization
Machining requires coordinating complex parameters for optimal efficiency and quality.
Researchers apply intelligent algorithms to analyze constraints and optimize parameters, improving production efficiency.
High-Speed Machining Process Assurance
CNC Machining Equipment
High-quality machining technology relies on coordinating cutting paths and tool selection to maintain machine efficiency and extend tool life, ultimately improving overall effectiveness.
The rigidity standards for the machine body are higher, and the rigidity requirements for the tool holder and spindle are also elevated.
The drive unit in cutting equipment should have high rotation speeds, and the axial distance between the tool and spindle should be maintained by the spindle, pressure, and cooling devices.

Cutting Tool Technology
Attention must be given to the installation, positioning accuracy, and assembly precision of the tool holder.
During machining, maintaining high speeds and preventing tool damage due to improper parameter selection is essential.
Cutting tool materials should be chosen based on specific requirements.
High-speed tool holders are suitable for high-speed cutting, featuring rapid expansion and contraction characteristics.
Moreover, during high-speed cutting, the tools must withstand high temperatures, high pressure, and external environmental impacts.
CNC Technology
Effective use of CNC technology, especially in developing efficient CNC programs to optimize processes, ensures that advanced CNC equipment meets production quality standards.
After planning, engineers should program CNC processes, select cutting parameters, and monitor machining status to ensure smooth operations.
Machine Operation and Maintenance
High-end intelligent CNC equipment requires proper operation and maintenance to ensure smooth process flow.
This is vital for producing high-quality products and achieving economic benefits.
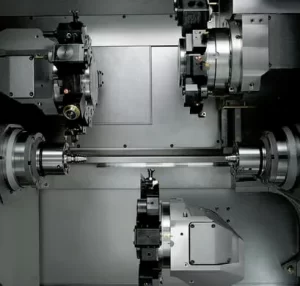
Conclusion
CNC machining is a key focus in metal cutting development.
Innovations are needed in intelligent manufacturing, cutting hard materials, tool design, process optimization, status monitoring, and equipment maintenance.