With the rapid development of technology and intensified competition in the global market, the manufacturing industry faces increasingly complex and rapidly changing challenges. Against this background, Rapid Prototyping Technology (RP) has become a powerful tool in modern manufacturing with its unique flexibility and efficiency.
Rapid prototyping technology shortens the product development cycle and opens up a new realm of design innovation and complex component manufacturing. This article will delve into the advantages and disadvantages of rapid prototyping technology. Through these analyses, we can better understand the role of rapid prototyping technology in modern manufacturing and its profound impact on the future of manufacturing.
What is Rapid Prototyping
Rapid Prototyping (RP) is a key prototype production method that quickly creates physical parts directly from CAD model data using various manufacturing technologies such as 3D printing, CNC machining, and injection molding.
RP technology improves product design at any stage, especially during new product development, through iterations and test data.
Its main purpose is to efficiently test design concepts and confirm their applicability, to identify and correct design defects before full production, minimize waste, and save time and cost.
Among rapid prototyping technologies, 3D printing has become mainstream because it can produce complex models in a small desktop space. Stereolithography (SLA), selective laser sintering (SLS), and fused deposition modeling (FDM) are the main 3D printing technologies.
Vacuum (polyurethane) casting and rapid injection molding are also popular RP technologies. These methods enable industrial designers and engineers to speed up product development cycles and ensure the accuracy and functionality of designs.
For example, Nike uses 3D printing technology to test the performance of different materials and structures to select the best materials and design solutions. This approach not only improves the performance of the product but also increases its durability and comfort level.
With rapid prototyping, companies can quickly evaluate the appearance and functionality of a product and make informed decisions about how the product will serve the end-user or the feasibility of manufacturing.
How Does Rapid Prototyping Process Work?
Detailed stages of the rapid prototyping process:
1. Design Creation: A digital 3D model of the object is created using CAD software. This stage is critical to laying the foundation for the prototype.
2. Data Preparation: The CAD model is processed and converted into a format suitable for the chosen Rapid Prototyping technology, usually an STL file.
3. Machine Setup: The rapid prototyping machine is prepared, calibrated, and loaded with the appropriate material (plastic, resin, or metal powder).
4. Prototyping: The machine builds the prototype layer by layer to the specifications of the CAD model.
5. Post-processing: Once the prototype has been built, post-processing is often required to achieve the desired surface finish or mechanical properties. This may include sanding, painting, or assembly.
Twenty advantages of rapid prototyping
Fast prototyping is a highly efficient method that offers countless benefits in the dynamic realm of design and development. This section takes an in-depth look at the twenty advantages
1. Accelerate the product development cycle
Rapid prototyping technology greatly shortens the time from design to physical product, speeding up product iteration.
2. Reduce development costs
It reduces the cost and human resource investment of traditional prototype manufacturing, especially in small-batch production.
3. Supports complex geometries
Capable of manufacturing complex internal structures and components with a level of precision and complexity that is difficult to achieve with traditional machining.
4. Increased Design Flexibility
Designers can test and modify designs more quickly to respond to market needs and user feedback.
5. Facilitates innovation and design optimization
Help designers find the optimal solution by quickly producing multiple versions of prototypes.
6. Supports Customized Production
Support personalized and customized production to meet the specific needs and preferences of different customers.
7. Reduces waste and environmental impact
Compared with traditional processing methods, it reduces material waste and energy consumption and meets environmental protection requirements.
8. Rapid verification and testing
You can quickly produce functional prototypes for testing and verification, which speeds up product launch time.
9. Improved product quality
Precise control of the manufacturing process improves product accuracy and consistency.
10. Simplify supply chain management
Reduce the time and risk of relying on external suppliers and increase production flexibility.
11. Enhance market competitiveness
Quickly respond to market changes, launch innovative products in advance, and gain a competitive advantage.
12. Agile production response
Able to quickly adjust production plans and production lines to adapt to changes in market demand.
13. Reduce product development risks
Quickly making and testing prototypes reduces the risks of product design and marketing.
14. Support diversified manufacturing needs
Suitable for manufacturing needs of various scales and industries, and flexibly respond to market changes.
15. Improve production efficiency
It reduces downtime and waiting time on the production line and improves overall production efficiency.
16. Promote engineering and medical innovation
Promote the application and innovation of new technologies in the fields of engineering and medical technology.
17. Increase the sustainability of production
Make the production process more environmentally friendly and sustainable by saving resources and energy.
18. Talent cultivation and technological development
Promote talent cultivation and technological research in areas related to rapid prototyping technology.
19. Expand new markets and applications
Open up new market opportunities and application areas, and promote the diversified development of the industry.
20. Improve customer satisfaction
Improve customer experience and satisfaction by providing products that are faster, more flexible, and more in line with personalized needs.
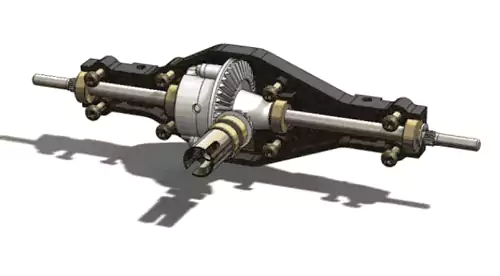
Disadvantages of rapid prototyping
Rapid prototyping technology offers many advantages, but it also has some drawbacks that cannot be ignored.
1. Limited material selection
Current materials for rapid prototyping have limited types and performance ranges, failing to meet all application needs.
2. Insufficient precision
Some rapid prototyping technologies cannot match the precision and surface quality of traditional methods, limiting high-precision products.
3. High cost
The cost of equipment and materials is high, especially in large-scale production, which may increase the overall cost.
4. Slow manufacturing speed
Compared with traditional mass production, the single manufacturing speed of rapid prototyping technology is slower, which affects production efficiency.
5. Complex post-processing
Some rapid prototyping technologies require complex post-processing processes, such as polishing and surface treatment, which increases the complexity and time cost of the manufacturing process.
6. Insufficient material strength
The strength and durability of some rapid prototyping materials are not as good as traditional materials, limiting their application in high loads and specific environments.
7. Design limitations
Current rapid prototyping technology cannot realize some complex geometric structures and functional designs, limiting innovation potential.
8. Environmental impact
Waste materials and emissions generated during the rapid prototyping process may have negative impacts on the environment and require effective treatment and management.
9. Technology dependence
The development and application of rapid prototyping technology depend on technological progress and innovation. Rapid technological upgrading may lead to obsolete equipment.
10. Demand for professional talents
Operating and maintaining rapid prototyping equipment requires professional skills and experience, which increases the company’s labor costs and training burden.
Conclusion
Through the above analysis of advantages and disadvantages, we can more comprehensively understand the role of rapid prototyping technology in modern manufacturing. As a flexible and efficient manufacturing process, rapid prototyping technology not only improves the speed and flexibility of product development but also makes it possible to manufacture complex geometric structures.
Current challenges include material selection, performance limitations, and precision surface quality. However, technology advancements and application experience will likely solve or greatly improve these issues.