Table of Contents
Rapid Prototyping (RP) has become an indispensable tool in modern product development, especially in the early stages of design. This technology accelerates the design validation process by rapidly generating functional prototypes and significantly improves the efficiency and quality of product development. With the continuous advancement of technology, rapid prototyping is applied to prototyping and gradually expanded to low-volume production and customization needs, which has become the key to enhancing market competitiveness. This article will discuss the advantages and benefits of rapid prototyping technology, revealing its essential role in accelerating product development, reducing costs, and optimizing design.
What is rapid prototyping?
Rapid prototyping uses advanced manufacturing technologies to produce prototype models during the design process, especially at an early stage. This method’s core purpose is to validate design decisions in the early stages of design by creating prototypes that functionally and cosmetically resemble the final product. Rapid prototyping helps designers quickly test and optimize their designs to ensure that the product meets expectations and can identify potential problems before formal production.
Essentially, rapid prototyping accelerates product development through the rapid production of high-fidelity prototypes. This technology not only verifies the functionality and appearance of a design through the testing of actual models but also provides a realistic assessment of materials, manufacturing processes, dimensional accuracy, and more. Rapid prototyping can help reduce the cost and time of later modifications, ultimately improving product quality and speeding up market launches.
Advantages and benefits of rapid prototyping
1. Accelerate product development and shorten development cycles
Time is a critical factor in the product development process. One of the most significant advantages of rapid prototyping is its ability to shorten product development cycles significantly. Traditional development methods usually require multiple design stages, manual prototyping, and repeated testing, which is often time-consuming. Rapid prototyping technology, however, generates physical prototypes directly from digitized design files almost within hours, greatly accelerating the process.
With this rapid feedback mechanism, designers can quickly obtain prototypes early in the design process for various tests and evaluations. For example, for several tests’ product form, function, and structure, designers can find potential problems as early as possible to avoid costly modifications later and promote product development quickly.
2. Reduce Product Development Costs and Waste of Resources
Rapid prototyping significantly reduces the upfront investment in product development compared to traditional manufacturing methods. Conventional methods require the manufacture of molds, tools, and unique production lines, all of which increase development costs. Rapid prototyping technology, on the other hand, directly uses digital design, 3D printing, and other methods to produce prototypes, eliminating the need for cumbersome mold manufacturing and equipment configuration. This reduces the initial investment, especially in the case of small batch production, which can significantly reduce development costs.
In addition, rapid prototyping can also reduce resource waste. In the traditional production process, a large number of materials are often necessary for trial and error, while through 3D printing and other means, designers can use less material to quickly produce prototypes, reducing unnecessary resource consumption and waste.
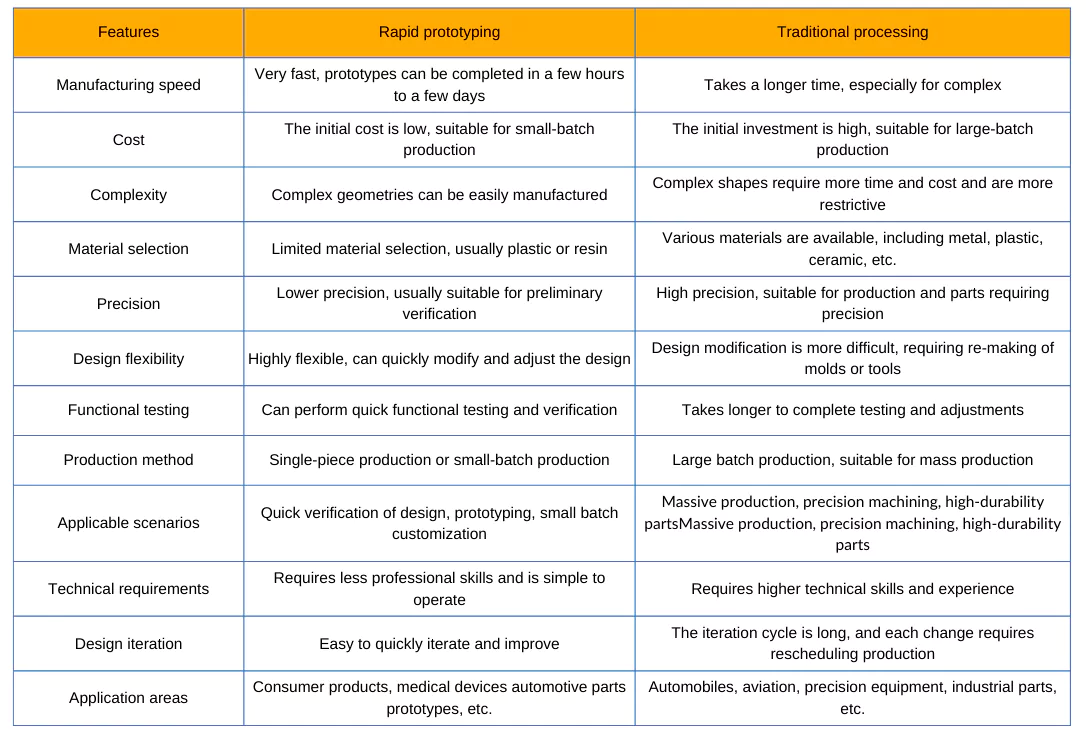
3. Supporting functional testing and verification to optimize designs
One of rapid prototyping’s biggest advantages is that it supports functional testing and verification. With the help of rapidly manufactured prototypes, designers can conduct several functional tests in the early stages of product development. This includes verifying structural strength, fitness for purpose, operability, and more to ensure that the design meets needs and fulfills functional requirements.
For example, when designing a new consumer electronics product, designers can quickly create a functional prototype and test various functions such as handholding comfort, button layout, display effect, etc. This allows designers to identify design flaws promptly and avoid significant problems in later production.
4. Increase User and Stakeholder Involvement
Traditional design verification is often only possible through drawings, images, or simple virtual models, which makes users and stakeholders feel less involved. Rapid prototyping provides a physical prototype that makes product design more intuitive and concrete. Stakeholders can more easily understand the product’s appearance and functionality and give more valuable feedback.
For example, during the development of a new product, customers or potential users can personally touch, operate, and feel the prototype, thus giving more accurate and practical advice. In this way, we cannot only improve the user’s sense of participation but also increase their trust and recognition of the product, further enhancing market acceptance.
5. Reduce the risk of product failure and avoid costly mistakes
Finding and fixing design flaws during product development is usually expensive, especially after the product has entered production. With rapid prototyping, designers can identify design problems early, thus reducing the risk of product failure.
For example, when manufacturing a complex mechanical component, designers can conduct functional testing and assembly verification through prototypes to ensure that all parts fit together smoothly. If problems can be identified and resolved early in the development process, not only can a lot of rework during production be avoided, but later repair costs and losses due to product failures can also be reduced.
6. Improve risk mitigation capabilities and increase development flexibility
Rapid prototyping technology can help companies identify and solve potential risks in the design in advance to enhance the flexibility of the product development process. Development teams often need help dealing with highly complex products or technological innovations. The flexibility of rapid prototyping allows designers to adjust their designs quickly, experiment with different solutions, and reduce the likelihood of risk in the development process.
In the face of fierce competition in the market or rapid changes in customer demand, rapid prototyping allows designers to flexibly adjust the design. This enables companies to optimize the design in a short period and quickly respond to market demand, thus improving overall development efficiency and market competitiveness.
7. Test multiple designs and materials to explore the best solution
Rapid prototyping also provides a powerful experimental platform where designers can test different designs and materials to find the optimal combination. This is especially important for highly innovative and experimental products to ensure that the final product meets performance requirements but is also optimized in terms of cost and production difficulty.
For example, when designing a new type of automotive part, designers can produce different material versions through rapid prototyping, including their strength, durability, and other aspects of the test, to select the most suitable material to improve the overall quality of the product.
8. Support ergonomic evaluation to optimize user experience
For many products, especially those that require close contact with people, ergonomic design is critical. Through rapid prototyping, designers can create ergonomic prototypes and evaluate them for comfort and fit. This plays a decisive role in ensuring the usability and user experience of the product.
For example, when designing a new cell phone or wearable device, designers can create prototype models and test their feel, ease of operation, and fit for the human body. This can help designers optimize the appearance and functionality of the final product and enhance the user experience.
9. Support small batch production to meet customization needs
Rapid prototyping is not only suitable for prototyping but also supports small-batch production. Rapid prototyping can provide flexible production capabilities for products that require customization or personalization to meet the needs of the small-lot output. This is critical for those who require high precision and customization of market demand and can help companies meet customer-specific needs while avoiding the high cost of mass production.
10. Parts integration and design optimization to simplify the manufacturing process
Through rapid prototyping, designers can optimize the integration of parts of the product and test and verify the coordination of each part. Especially for complex products composed of multiple parts, rapid prototyping can help designers verify the structure of the parts in the early stages to ensure that the final design is more concise and efficient and reduce unnecessary processes in the production process.
Conclusion
The widespread use of rapid prototyping has not only changed the way products are developed. Still, it has also significantly improved the efficiency and flexibility of companies in design, verification, and production. Rapid prototyping helps companies adapt to changing market demands by speeding up product development, reducing costs, supporting functional testing, optimizing design, improving user engagement, and minimizing production risks. It ensures that their products meet user needs more quickly and accurately. In today’s competitive market, rapid prototyping is a key innovation tool that enables faster product iteration, and optimization and supports high-quality, efficient production.