Table of Contents
CNC machining refers to a process method that uses digital devices and information to control the movement of parts and cutters to process the parts on a CNC machine.
It is an effective way to solve the variable rapid prototyping components, small batch parts, complex shape parts and high CNC precision machining components and achieve high efficiency parts.
What is CNC machining ?
CNC machining is a machining method that uses digital devices and information to control the displacement of parts and tools to process parts on CNC machines.
It is an effective way to solve variable rapid prototyping components, small batch parts, complex shape parts, and high CNC precision machining parts and achieve high efficiency parts.
A CNC machine combines mechanical systems and numerical control technology to efficiently process complex-shaped workpieces.
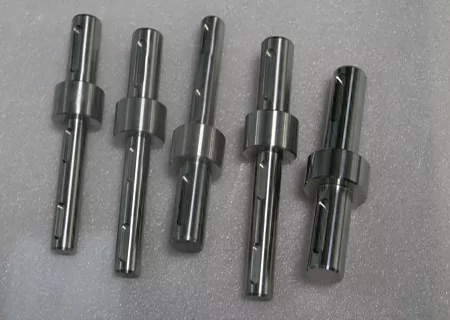
How does CNC machining work?
Design and Programming
Use computer-aided design (CAD) software to create a three-dimensional model of the workpiece, including the geometry and dimensions of the part.
The user imports the CAD model into computer-aided manufacturing (CAM) software, and the CAM software generates numerical control codes (G codes) that contain machining parameters such as tool paths, cutting depths, and feed speeds.
Machine Preparation
The operator fixes the workpiece on the worktable of the CNC machine and installs the required tools, such as milling cutters, turning tools, or drills.
The operator calibrates the machine tool to determine the reference point (zero point) of the workpiece so that it is aligned with the coordinate system in the NC program.
Perform processing
The operator transmits the NC program to the machine tool through the machine tool controller, and the controller controls the movement of the machine tool according to the program instructions.
The CNC machine tool processes the workpiece according to the preset tool path, removing material layer by layer through operations such as cutting, milling, and drilling to form the final part shape.
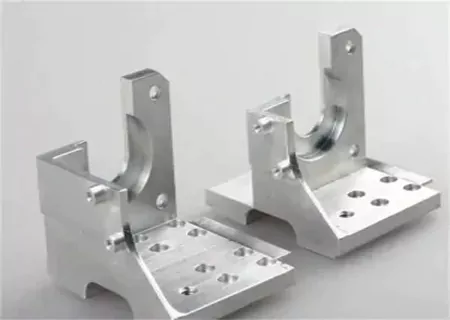
Inspection and Quality Control
Based on the test results, the operator carries out subsequent processing or correction if necessary to achieve the expected accuracy standard.
Different Types of CNC Machines
The earliest CNC machines date back to the 1940s, when electric motors were first used to control the movement of existing tools.
As technology advanced, engineers enhanced the mechanisms with analog computers and eventually digital computers, giving rise to CNC machining.
The vast majority of today’s CNC equipment is fully electronic.
Some of the more common CNC processes include ultrasonic welding, drilling, and laser cutting. The most common machines used in CNC systems include:
CNC Milling Machines
Lathes
Plasma Cutters
Electrical Discharge Machining Machines
Electrical Discharge Machining (EDM), also known as Die Machining and Spark Machining, is a process that uses electrical sparks to shape a workpiece into a specific shape.
During the EDM process, an electric current discharge occurs between two electrodes, which removes certain parts of the workpiece.
When the space between the electrodes becomes smaller, the electric field becomes stronger and therefore stronger than the dielectric.
This allows the current to pass between the two electrodes.
Therefore, each electrode removes a part of the workpiece. Subtypes of EDM include:
Wire EDM: Wire EDM uses spark etching to remove parts of electronically conductive materials.
Sinking EDM: Sinking EDM uses electrodes and workpieces immersed in a dielectric fluid to form the workpiece.
During the flushing process, the liquid dielectric carries away debris from each finished workpiece after the current between the two electrodes stops, thereby eliminating any further charge.
Waterjet Cutting Machines
In CNC machining, a waterjet is a tool that uses high-pressure water to cut hard materials such as granite and metal.
In some cases, operators mix the water with sand or other powerful abrasive substances.
Companies often use this process to shape factory machine parts.
Operators can use waterjet as a cooling alternative for materials that cannot withstand the high heat of other CNC equipment.
Due to the cooling properties of waterjet, several industries such as aerospace and mining rely on waterjet for engraving and cutting, etc.
Companies also use waterjet cutters for applications that require very intricate cuts in materials, as the lack of heat prevents any changes that metal-on-metal cutting may cause to the inherent properties of the material.
History of CNC machining
Before the introduction of Computer Numerical Control (CNC), the manufacturing process involved intense human labor, unnecessarily long production runs, wasted material, and was fraught with pitfalls.
Today technology has dramatically improved the manufacturing process.
The introduction of CNC machining technologies offers a high level of reliability, making iterative processes more automatic. But what is CNC machining?
What products can manufacturers make using CNC technology? How does CNC machining work, and what materials can manufacturers use in manufacturing processes that use CNC machines?
The needs of the aviation industry gave birth to CNC machining technology.
In the late 1940s, an American helicopter company proposed it.
The original idea of CNC machine tools, the Massachusetts Institute of Technology developed a three-axis CNC milling machine in 1952.
Manufacturers used this type of CNC milling machine to process aircraft parts in the mid-1950s.
In the 1960s, CNC machining prototypes and programming work became increasingly mature and refined.
Various industries have used prototype CNC machining services, but the aerospace industry has always been the largest user of CNC machine tools.
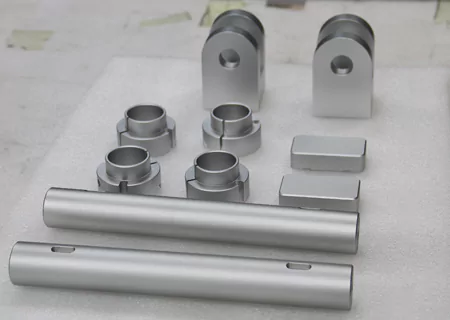
Some large aircraft factories equip themselves with hundreds of CNC machine tools, with cutting machines being the main ones.
CNC machined parts include integral wall panels, beams, skins, bulkheads, propellers, aircraft engine housings, shafts, discs, blades and unique combustion chamber cavity surfaces liquid rocket engine.
The initial stage of the development of CNC precision machining is based on continuous path CNC machine tools, continuous path control.
Conclusion
CNC machining, or Computer Numerical Control, is a technology that uses computer programming to control machine tools to automatically perform precision cutting, milling and other operations.
Manufacturers widely use it in the manufacturing industry.
By precisely controlling the tool path, it can achieve high-precision processing of materials such as metals and plastics.
It is suitable for producing parts with complex shapes and strict dimensional requirements.