CNC milling technology occupies an important position in the field of machining with its high precision, high efficiency and high flexibility.
Spiral milling is an advanced cutting process in CNC milling, which realizes continuous and efficient machining of the workpiece through the spiral feed of the tool in the axial direction, with the advantages of high machining efficiency, good surface quality and high dimensional accuracy .
Overview of spiral milling technology
Technical principle
The principle of spiral milling technology is that the tool rotates in the axial direction, and the workpiece is fed along the forward direction of the tool, forming a continuous spiral cutting trajectory.
In the CNC milling machine, this movement process is realized through the high-precision control of the CNC system, which guarantees the precise and accurate movement of the tool and the workpiece.
Specifically, the CNC system will adjust the rotational speed, feed speed and cutting depth of the tool in motion in real time according to the preset program, so that the tool gradually cuts the material on the surface of the workpiece along the preset spiral path.
Technical Advantages
In CNC milling processing, spiral milling technology shows significant application advantages.
Take thread processing as an example, modern CNC machine tools in the thread milling cutter made of carbide, processing line speed of 80 ~ 200 m-min-1, while the traditional high-speed steel tap processing line speed is only 10 ~ 30 m-min-1.
In other words, in the same time, spiral milling can complete more cutting volume.
Compared with the traditional tapping process, spiral milling technology has obvious advantages.
A higher line speed allows for quicker completion of machining tasks, enhancing efficiency.
Spiral milling achieves high-precision machining while minimizing errors, improving accuracy.
Carbide thread milling cutters last longer than HSS taps, and spiral milling enhances the surface finish, resulting in a smoother workpiece.
In summary, spiral milling technology has an important position in CNC milling processing, which provides a strong guarantee for improving processing quality and efficiency, and is an indispensable advanced technology in modern CNC processing, which is worth promoting.
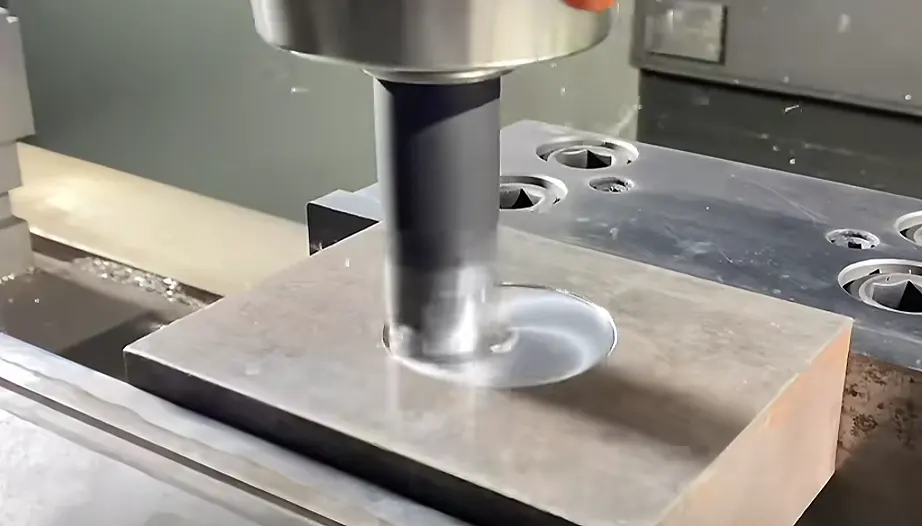
Use of spiral milling technology in CNC milling processing
Complex surface processing of workpiece
Spiral milling technology in the workpiece complex surface processing application effect is good.
Take the automobile engine block as an example, its internal surface is complex and difficult to process.
Traditional machining technology struggles with complex workpieces and often proves ineffective.
In contrast, spiral milling technology adapts to different surface shapes through the helical movement of the tool, enabling precise machining of complex surfaces inside the engine block while maintaining surface quality and productivity.
In the actual machining process, the tool cuts along the helical path and realizes continuous helical feed in the axial direction.
This cutting method can promote relatively uniform cutting force distribution, which helps to reduce vibration and cutting heat.
Improved Cutting Performance and Efficiency
When machining complex curved surfaces of workpieces, the machining efficiency of helical milling technology can be increased by about 30% compared with the traditional straight milling technology.
Traditional straight milling technology requires multiple tool adjustments, such as adjusting tool paths and cutting parameters, when machining complex surfaces, resulting in lower machining efficiency;
Spiral milling technology can reduce unnecessary tool parameter adjustment time through continuous spiral feed, and significantly increase the machining speed.
Enhanced Surface Quality
In terms of workpiece surface roughness, helical milling technology can reduce the roughness Ra of the workpiece surface from the traditional straight milling of 1.6 μm to 0.8 μm, improving the overall machining quality.
A smooth surface not only improves the aesthetics of the workpiece, but also ensures that the workpiece has good performance and reliability during use.
Utilization of workpiece thread processing
When processing workpiece threads, it is necessary to cut the processing components, the operation process is more complicated, and the requirements for processing accuracy are high. In workpiece thread processing, spiral milling technology can show high precision.
High Precision in Thread Machining
For example, in the processing of M40×1.5 threads, the application of spiral milling technology can fully utilize the three-axis linkage function of CNC machine tools.
During machining, the tool cuts along the carefully planned spiral trajectory, rotates 360°, and then continues machining one pitch up in the axial direction. Such a machining trajectory creates an extremely precise thread structure.
If a carbide thread milling cutter is used for helical milling, with a cutting speed of 250 m – min-1 and a feed rate of 0.1 mm – r-1, threads can be machined with an accuracy of ISO 6H.
This level of precision can meet the process accuracy requirements in both the precision machinery manufacturing field and the aerospace field, which requires extremely high thread precision.
Enhanced Efficiency and Tool Longevity
In terms of processing efficiency, the traditional tap tapping processing method is susceptible to a variety of factors during thread processing, such as uneven distribution of cutting force, poor chip removal, etc., resulting in a decline in processing efficiency.
Spiral milling technology with its unique cutting method, can increase the processing efficiency by about 5 times.
Spiral milling technology adopts rotary tools for cutting, the cutting force can be more evenly distributed on the tool, reducing the tool wear and workpiece deformation caused by the concentration of cutting force.
At the same time, the technology in the process of machining can be very good chip removal, to avoid the accumulation of chips and affect the machining accuracy and efficiency.
Spiral milling technology can also be adjusted according to different processing requirements to adjust the parameters, to meet the needs of a variety of complex workpiece thread processing, adaptability is stronger.
Versatility in Large-Diameter and Non-Standard Thread Processing
In addition, the use of spiral milling technology can solve the traditional processing methods in the processing of large-diameter high-precision thread problems.
Traditional processing technology in the processing of some large-diameter high-precision thread workpiece, often need to use large-scale equipment and complex process system, and it is difficult to ensure the final processing accuracy.
Spiral milling technology can easily cope with the processing of large-diameter threaded workpieces, realizing the efficient processing of threads with multiple rotations (left-handed, right-handed) and different pitches (lead), especially in the processing of non-standard threads, which is more advantageous.
Application of deep hole machining for workpieces
Deep hole machining, especially in aerospace and other high-precision areas of large, long and thin hole machining, there are problems such as poor chip removal, cutting heat accumulation, tool vibration, etc., affecting the processing efficiency and quality.
The use of spiral milling technology can effectively solve the problems in deep hole machining.
Take the deep hole machining of a key aerospace part as an example, the hole depth of the part reaches 300 mm, which puts forward strict requirements for machining accuracy and surface quality.
When using thread milling technology for deep hole machining, the tool under the precise control of the CNC system, according to the preset helix path slowly into the hole, in a helical way for cutting processing.
This cutting method not only avoids the cutting force mutation and vibration problems generated by linear feeding, but also optimizes the chip discharge conditions during the cutting process.
In the cutting process, chips will be discharged smoothly along the spiral trajectory, preventing chips from gathering in the hole, avoiding the second friction and wear of the tool and chips, and guaranteeing the stability of the tool and the consistency of machining accuracy.
In actual processing, the spiral milling technology can be used in the cutting speed of 100 m – min-1, feed rate of 0.05 mm – r-1 conditions, the surface roughness of the deep hole Ra control below 1.2 μm.
Spiral milling technology shows superior performance in deep hole machining, which can meet the severe machining requirements of aerospace parts.
Thanks to the effective control of cutting heat and the smooth discharge of chips, the service life of spiral milling tools is nearly one times longer than that of traditional machining processes, and significantly reduces production costs and improves processing efficiency.
Spiral milling process of the use of key points
Standardize tool selection and management
Tooling is an indispensable tool in spiral milling process.
The selection and management of tools will directly affect the subsequent machining efficiency and the machining quality of the final product.
In the process of tool selection, it is necessary to comprehensively consider the material, shape, size and processing needs of the workpiece.
For example, for hard-to-cut materials such as cemented carbide or titanium alloys, tools with high hardness and high wear resistance should be selected, such as cemented carbide spiral milling cutters and diamond coated tools.
The geometric angle of the tool such as the front angle, back angle, helix angle, etc., is also an important factor to be considered when selecting.
The geometric angle of the tool needs to be determined according to the specific processing needs, to reduce the cutting force, reduce the cutting temperature as the main goal, while taking into account the improvement of processing surface quality.
In the process of tool utilization, extra attention should be paid to tool wear monitoring and replacement.
On the one hand, we should set a relatively reasonable tool life standard, on the other hand, we should use the tool wear detection function in the CNC system to realize the dynamic monitoring of the tool operation status.
If the tool is used in the process of running out of the predetermined range of wear, to immediately stop machining and replace the new tool, so as not to reduce the quality of machining or machine accidents due to tool wear.
Reasonable setting of cutting process parameters
From the process point of view, the cutting process parameters set is the key link in the spiral milling process.
Cutting parameters include cutting speed, feed rate, depth of cut and tool path. The setting of these parameters needs to take into account the workpiece material, tool type and processing requirements and other factors.
Take deep hole machining as an example, the selection of cutting speed needs to take into account the heat resistance of the tool and cutting efficiency, generally controlled at 100 ~ 200 m – min-1;
Feed rate should be determined according to the rigidity of the tool and cutting stability, usually choose a lower feed rate to ensure machining accuracy and surface quality;
Depth of cut should be determined according to the cutting ability of the tool and the machining allowance to avoid one-time cutting too deep resulting in tool damage or reduced machining quality;
Tool paths need to be gradually optimized through the programming function of the CNC system.
Through the CNC system, you can realize the precise control of the tool path and cutting parameters of the dynamic adjustment, thus further improving the processing efficiency and processing quality.
Focus on cooling lubrication and chip removal
In the spiral milling process, cooling lubrication and chip removal should not be ignored.
In the process of machining, the cutting area will inevitably produce a large amount of cutting heat and chips, if there is no effective cooling lubrication and chip removal at the first time, it will lead to increased tool wear, which will lead to reduced machining quality and even machine accidents.
Therefore, in the spiral milling process, it is necessary to use reasonable cooling and lubrication to reduce the cutting temperature and cutting force.
The use of coolant can cool the tool well. The selection of coolant type and concentration should take into account the workpiece material and processing needs.
For example, in the processing of difficult-to-cut materials, high-performance coolant can be used to reduce cutting heat, improve cutting efficiency and processing quality;
In the processing of extremely high precision requirements of the workpiece, you can choose a low-viscosity coolant, in order to reduce the residue in the cutting area.
Lubrication methods include spray lubrication, oil mist lubrication, etc., can be selected according to actual needs. In addition to cooling lubrication, but also to design a more scientific chip channel and chip removal device to ensure that the chips are discharged smoothly.
Optimize the tool path
Tool path in the spiral milling process is very critical, its optimization can not only directly improve the processing efficiency, but also help to extend tool life and maintain machining accuracy.
In practice, the optimization of the tool path needs to carefully consider the geometric characteristics of the workpiece, including but not limited to shape complexity, size range and material properties, and need to consider the specific processing needs, such as precision requirements, surface finish and so on.
Complex surface machining of aluminum alloys in the aerospace industry, for example, is particularly delicate in terms of tool path planning.
In order to meet the requirements, it is necessary to use advanced CAD/CAM software, such as Siemens NX or Mastercam, to carry out three-dimensional modeling of the workpiece and generate a preliminary tool path based on the model data.
On this basis, a layered milling strategy is implemented to decompose the complex surface into multiple manageable layers, with the thickness of each layer controlled at 0.5 to 2.0 mm, depending on the curvature of the surface and the hardness of the material.
The layering strategy significantly reduces the load of a single cut, reduces tool wear, and ensures a smooth transition of the machined surface.
Strengthen process monitoring and adjustment
In the spiral milling process, strict process monitoring should be implemented, which is the key to guarantee the processing quality and efficiency.
Modern machining shops generally use intelligent machine tools integrated with sensors and data analysis systems, these CNC machines can monitor cutting force, cutting temperature, vibration and other key parameters in real time, providing timely feedback for personnel.
In addition, customized scripts written in data analytics software, such as MATLAB or Python, are used to dig deeper into the monitoring data, enabling the identification of potential problems and trends in the machining process, such as accelerated rates of tool wear and a sustained rise in cutting temperatures.
Based on this early warning information, operators can take precautions such as changing tools, adjusting coolant flow or optimizing cutting parameters to ensure that the machining process is at its optimum.
After machining is completed, operators need to carry out strict dimensional measurement of the workpiece (using a CMM with an accuracy of ±0.005 mm), shape accuracy assessment (contour detection, etc.) and surface roughness testing (using a surface roughness meter with an accuracy of 0.1 μm).
This is a critical step to ensure that the machining quality meets the design requirements.
If deviations are found, the causes need to be immediately analyzed and targeted improvement measures taken to provide valuable experience for subsequent processing and ensure production stability and reliability.
Conclusion
In the environment of rapid development of modern manufacturing industry, spiral milling technology has a high application value in CNC milling processing, which helps to improve the effect of CNC milling processing.
The application of spiral milling technology can improve the continuity and efficiency of workpiece processing, and promote the high-precision development of the mechanized processing industry.
Technical operators should continuously strengthen the understanding of spiral milling technology in CNC milling processing and apply it to actual processing.
FAQ:
Spiral milling is an advanced technique in CNC milling where the cutting tool moves in a helical (spiral) path along the axial direction. This method ensures high machining precision, better surface quality, and improved efficiency compared to traditional straight-line milling.
Spiral milling plays a vital role in CNC machining due to its ability to provide high-speed, high-precision, and continuous cutting. It reduces tool wear, enhances surface finish, and increases overall machining efficiency, especially in complex part geometries and deep hole machining.
In CNC thread machining, spiral milling allows the tool to follow a controlled helical trajectory, producing accurate threads with minimal error. Compared to traditional tapping, it offers higher speed, longer tool life, and better chip evacuation, ensuring precise thread profiles even for large or non-standard threads.
Spiral milling outperforms traditional tapping with higher line speeds (up to 250 m/min), better tool life using carbide tools, reduced vibration, and improved chip removal. It also minimizes deformation and increases accuracy, especially in high-precision industries like aerospace.
Yes, spiral milling is highly effective for deep hole machining in CNC operations. Its continuous helical feed improves chip removal, reduces cutting heat, and minimizes tool vibration, making it ideal for aerospace parts with hole depths exceeding 300 mm.
Spiral milling reduces surface roughness by maintaining a stable cutting path and minimizing vibration. It can lower Ra values from 1.6 μm (straight milling) to 0.8 μm or less, resulting in smoother surfaces and improved workpiece reliability and aesthetics.
Absolutely. Spiral milling is well-suited for machining complex surfaces such as engine blocks. The helical tool movement adapts to varying surface geometries, allowing precise cuts with uniform force distribution, reduced heat buildup, and better surface integrity.
Key parameters include cutting speed (100–250 m/min), feed rate (0.05–0.1 mm/rev), cutting depth, and optimized tool paths. Proper tool geometry and cooling systems are also critical to achieving precision, efficiency, and tool longevity in spiral milling operations.
Spiral milling distributes cutting forces evenly along the tool path, reducing localized stress. With effective cooling and chip evacuation, it minimizes heat buildup and friction, resulting in lower tool wear and up to twice the service life compared to conventional methods.
Yes, spiral milling excels in processing large-diameter and non-standard threads. It eliminates the need for specialized large-scale equipment by using CNC-controlled helical paths, offering precision and flexibility in diverse thread types with various pitches and handedness.