Sheet metal parts make up the framework and aerodynamic shape of the aircraft fuselage. They are essential components of the aircraft. The number of these parts is large, accounting for 50% of the total parts in the aircraft. These parts come in many varieties, have complex shapes, and require high quality. Additionally, the processing difficulty is significant.
Sheet metal parts manufacturing technology is a key technology. It helps the aircraft achieve both structural efficiency and excellent performance. It is also one of the pillars of aerospace manufacturing engineering. The degree of advancement in this technology is an important measure of a country’s aerospace manufacturing capacity and significance.
In recent years, countries have introduced new-generation aircraft. This has driven the development of aviation manufacturing technology. Sheet metal manufacturing technology has also advanced significantly.
Super Plastic Forming / Diffusion Bonding
Superplastic Forming/Diffusion Bonding (SPF/DB) is a method used to manufacture monolithic structures with hollow interlayers. This method uses materials that possess both superplasticity and diffusion bonding within a specific temperature range.
It completes superplastic forming and diffusion bonding in a single thermal cycle. The forming method improves the overall structure of the manufacturing technology with almost no margin.
SPF/DB is an advanced technology for manufacturing near-surplus-free monolithic structural components. Its in-depth development and wide application have significantly impacted the design and production of modern aerospace structures.
The U.S. regards it as the high-efficiency, cost-effective manufacturing technology for large, complex structural components in the 21st century. SPF/DB has several technological advantages, including:
(1)High Part Economy
SPF/DB can replace many parts originally requiring mechanical connections or welding. This greatly reduces the number of parts and fixtures. It shortens the manufacturing cycle and reduces costs.
(2)Good Structural Integrity
The diffusion connection in SPF/DB eliminates the interface. This creates a unified structure and greatly improves fatigue and corrosion resistance.
(3)Manufacturing of Complex-Shaped Parts
SPF/DB can form parts with complex shapes that are hard to achieve. The material in the superplastic forming process can withstand significant deformation without rupture. For example, a titanium plate can form parts with small bending radii and thick material, which conventional cold-forming methods cannot achieve or would require multiple forming steps.
(4)Design Flexibility
SPF/DB offers a wide range of material choices. This increases design flexibility, allowing for the combination of different material advantages. Designers can also use hollow sandwich structures to optimize load-carrying efficiency and reduce weight, meeting diverse application needs.
(5)Small Flow Stress
The material’s flow stress in superplastic forming is very low. This allows the use of small tonnage equipment to form large structural parts. The processed parts have no rebound, no residual stress, and high forming accuracy.
SPF technology was first introduced in the early 1930s. As the demand for lightweight, long-life, high-strength, and high-stiffness components increased in aerospace manufacturing.
SPF/DB technology went through three stages: basic process research in small laboratories, engineering application research on typical structures, and production application and development of complex structures.
Currently, SPF technology is widely used in aerospace engineering. For example, the F-15 contains over 70 SPF/DB structural parts.
The F-18 uses more than 20 titanium alloy SPF/DB structural parts. SPF/DB combined structures are also used in the F-22, such as the rear fuselage titanium alloy superplastic forming/diffusion connection heat shield.
Using SPF/DB structural parts can reduce the weight of the aircraft by 10% to 30%. It also reduces costs by 25% to 40%.
The development of SPF/DB components ranges from small to large sizes. For example, the U.S. F-22 rear fuselage uses eight high-strength titanium alloy SPF/DB heat shields, each measuring 915mm × 635mm × (1mm ~ 4mm). The B-2 aircraft has titanium alloy SPF/DB parts measuring 1200mm × 3600mm × 6.3mm.
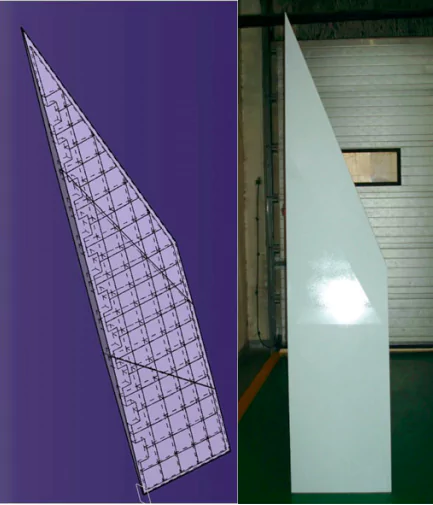
Fig. 1 SPF/DB building blocks for hollow-solid hybrid structures
Shot Peening Technology
Shot peening technology uses high-speed projectiles to impact the surface of the metal plate. This impact causes plastic deformation of the surface material, extending it in all directions.
As a result, the surface area increases. The material deformation is restricted by consistent limitations, which causes the plate to bend. This method is one of the main ways to form wall plate parts.
The main features of shot peening forming technology include:
(1)Low cost of parts manufacturing:
It does not require forming molds. The process equipment is simple, and the process preparation cycle is short.
(2)Strong fatigue resistance in formed parts:
The parts exhibit residual compressive stress, which enhances their performance.
(3)Wide range of forming capabilities:
The size of the part is not limited by the blast chamber specifications. Shot peening can form skin wall plates of varying thickness. It can also form ribbed, overall wall plates. Additionally, it can create parts with simple single curvatures or more complex double curvatures.
Shot-peened part designs have evolved. Initially, designers created simple shapes. Now, they design more complex curved structures with varying thicknesses, both uniform and non-uniform. The sizes of parts have also increased.
Currently, shot peening has become a mature and specialized method of wall plate processing at companies like Boeing, Airbus, and Metal Improvement.
Shot peening technology can form wall plates as long as 35 meters. It can also create parts with bending and torsion, such as saddle-shaped complex surfaces. The technology can form various structural components, including mouth covers, tabs, reinforced edges, miters, reinforcements, short cross bars, and other combinations of complex structures.
Figure 2 shows the use of pre-stressed shot peening technology by the U.S. Metal Improvement Corporation. They used it to manufacture the A380 supercritical wing’s under-wall plate. This is the largest part formed by shot peening, with the longest length and the greatest thickness achieved so far.
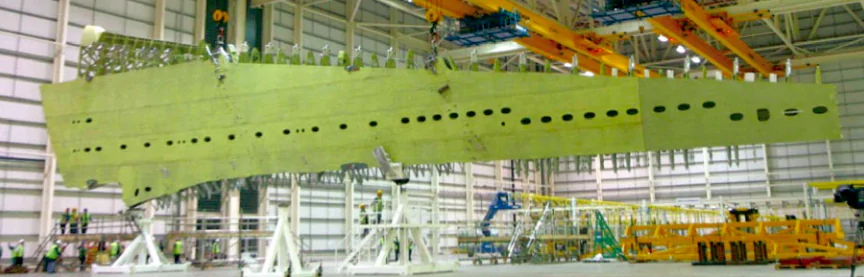
Fig. 2 Airbus A380 aircraft and its shot peening of the outer wing under the wing surface of the whole wall plate
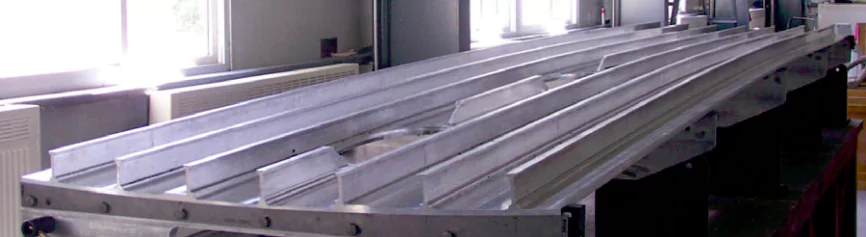
Fig.3 Shot peening of a reinforced monolithic wall plate process validation part
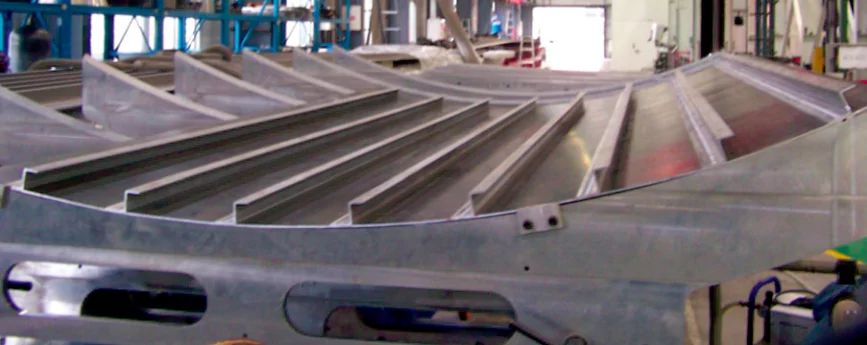
Fig. 4 Simulation of a welded reinforced monolithic wall plate with shot peen forming
Spinning technology
Metal spinning forming technology refers to rotating the blank and the core mold or rotating the spinning tool around the blank and the core mold.
The spinning tool and core mold move relative to each other. This process applies pressure to the blank, creating continuous, point-by-point deformation.
It is mainly used for processing thin-walled rotary body workpieces.
Spinning technology is a typical continuous local pplastic-formingprocess. It allows manufacturers to produce thin-walled rotary parts with minimal cutting.
This advanced manufacturing technology has wide applications in machinery, electronics, the chemical industry, automotive, aerospace, and the defense industry.
For example, manufacturers use spinning technology for parts like the nose cone of the space shuttle, screw isolation catchers, the outer receiver of aero-engines, exhaust cones, missile cowls, and guidance modules.
The main advantages of spinning technology include high material utilization, precise product dimensions, good organizational performance, and excellent process flexibility.
It also allows for easy mechanization and automation, long mold life, and lower production costs.
As aerospace and other high-tech industries grow rapidly, the demand for lightweight, integral, and complex thin-walled rotary shell parts increases.
These parts also have higher performance requirements. Spinning technology has evolved to meet these needs. The advancements are mainly seen in the following areas:
(1) Increase in difficult-to-process materials
High-strength aluminum alloys, titanium alloys, and high-temperature alloys are harder to deform.
As a result, hot-spinning technology has been developed to process these materials.
For instance, the Beijing Aviation Manufacturing Engineering Research Institute used high-temperature alloys to develop an aircraft engine magazine shell. This replaced the original forging process.
They studied how temperature affects the deformation of high-temperature alloys and developed process parameters, such as mandrel speed, spinning wheel feed speed, and temperature control.
This approach solved key challenges like temperature control and forming quality, reducing the need for subsequent machining and improving the mechanical properties of the parts.
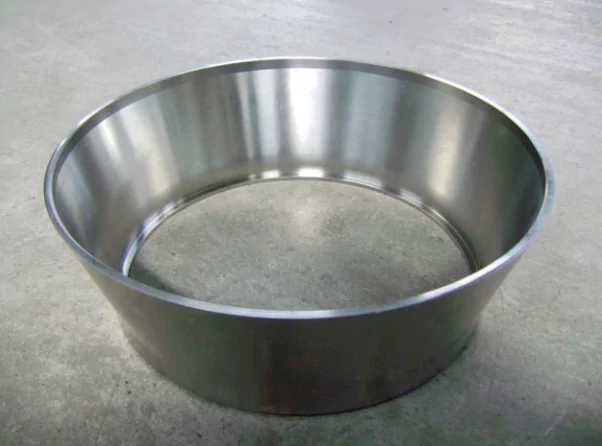
Fig. 5 Spinning forming an engine magazine shell
(2) Demand for large-size, high-precision complex thin-walled parts
The demand for large, complex thin-walled parts with high precision continues to grow. Multi-pass composite spinning is becoming increasingly refined.
For example, Northwestern Polytechnical University used a combination of numerical simulation and experimental methods to study the relationship between uneven plastic deformation, forming defects, and the impact of blanks, process, and mold parameters.
This research helped achieve the precise forming of large, complex thin-walled shells with internal reinforcements.
Hot forming technology
Hot forming technology manufactures sheet metal parts. In this process, the part blank is stamped and formed at high temperatures. The technology uses metal materials, which are heated to soften.
This heating reduces the material’s deformation resistance, improves the forming limit, reduces elastic rebound, and increases forming precision.
It mainly applies to titanium alloy, magnesium alloy, molybdenum alloy, and other materials that are hard to deform at room temperature.
The main process methods include bending, deep drawing, expansion, flanging, turning holes, and local forming.
Since the 1950s, the large number of titanium alloy applications in aerospace and military industries has driven the rapid development of hot forming technology.
This technology soon entered the engineering application stage.
Today, military aircraft, civilian aircraft, aircraft engines, missiles, and other manufacturing areas widely use hot-forming technology.
For example, it is used to make parts like aircraft fuselage skin, tail fairing, spacer frame, engine nacelles, hot end parts, adapter sections, missile shells, and wings (Fig 6).
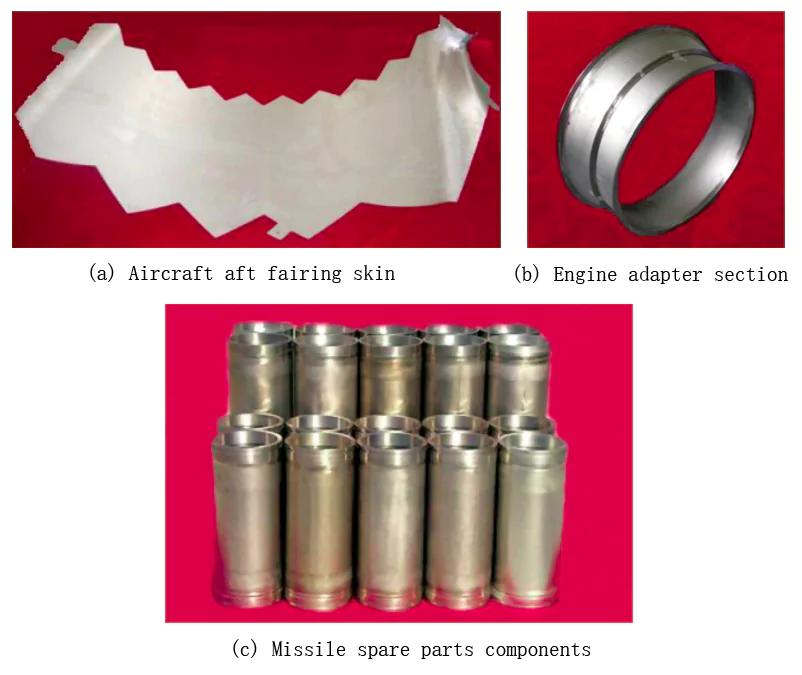
Fig. 6 Typical thermoformed parts
Currently, the long lifespan of civil aircraft, the lightweight design of military aircraft with high stealth, and the increasing demand for faster missile flight speed are driving the need for better performance. To meet these requirements,hot-formingg technology continues to innovate. This innovation mainly reflected in:
(1)large size:
There is no spare parts assembly demand. The team enhances the precision control of thehot-formingg shape. Large-size parts cause significant rebound.
The team faces challenges in correcting thermal expansion between the parts and the mold. The requirements for the profile and external dimensions of the parts are stricter without spare parts assembly.
For example, Beijing Aviation Manufacturing Engineering Research developed a complex TC4 titanium alloy aft fuselage upper wall plate for a specific type of aircraft.
The part has torsion and double curvature, making it difficult to form. The project team studied the high-temperature deformation behavior of TC4 titanium alloy materials.
They established a thermal material constitutive model and used numerical simulation technology. This helped them predict the rebound of the parts successfully.
They also conducted material-forming limit tests and created a thermal-forming limit curve.
Based on this, they modified the mold. This led to successful large-scale molding of the fuselage.
The team corrected the mold. They accurately formed the large and complex titanium alloy parts in the hot state.
(2) Diversification of materials:
Expanding the field of application of hot forming: As the service environment temperature of parts increases, manufacturers must use new materials.
For example, a certain type of missile now reaches a flight speed three times the speed of sound. The service temperature of its parts can be as high as 400℃. Ordinary TC4 material cannot meet the needs at this temperature.
Beijing Aviation Manufacturing Engineering Research focuses on studying new materials, such as TNW700 hot forming technology. The research will contribute to advancing China’s titanium alloy technology.
(3)Automation and Intelligent Level Enhancement:
As science and technology progress, automation and intelligence drive the development of hot-forming technology.
Advanced CNC machine tools and robotics achieve precise control of the hot-forming process. These technologies also reduce errors caused by human operations.
IoT technology enables real-time monitoring of material temperature, pressure, and forming process parameters. This ensures the stability of the production process and the quality of the finished product.
For example, the Beijing Aviation Manufacturing Engineering Research Institute has automated the entire process, from material preheating to forming and cooling.
They established an intelligent hot-forming production line, which has significantly improved production efficiency and part consistency.
(4)Integration of green manufacturing concept:
As environmental problems become more severe,hot-formingg technology is transforming into green manufacturing.
The team optimizes process parameters and uses renewable materials to reduce energy consumption and waste generation. This approach leads hot-forming technology toward sustainable development.
For example, in the production of a certain type of civil aircraft, the project team improved the forming process to reduce heat loss. They also used a more environmentally friendly cooling medium, which reduced the environmental impact.
This green manufacturing concept improves production efficiency. It also helps achieve sustainable development in the aerospace sector.
Ultrasonic processing technology
Ultrasonic machining technology is an advanced technology. It uses high-frequency ultrasonic vibration to machine materials.
The technology sends ultrasonic energy to the cutting tool. This causes the tool to vibrate when it contacts the material. The vibrations reduce the cutting force. They also improve cutting efficiency, machining accuracy, and surface quality.
Ultrasonic machining works well with hard and brittle materials, such as ceramics, glass, and certain metal alloys. It is widely used in aerospace, microelectronics, and medical devices.
(1) Precision machining capability:
Ultrasonic machining achieves high-precision microfabrication. It is suitable for manufacturing complex shapes and precision parts.
Its vibration effect reduces the cutting force. This reduces material damage and improves the quality of the finished product.
For example, in the aerospace field, manufacturers commonly use ultrasonic machining. They use it to make high-precision aircraft engine components and turbine blades.
(2) Material diversity:
Various materials, including metals, plastics, and composite materials, use the technology. As new materials emerge, ultrasonic processing technology continuously expands its application field.
For example, ultrasonic processing can reduce the processing difficulty and enhance the performance of special alloys or new composite materials.
(3) Automation and intelligence:
Science and technology have developed rapidly. Ultrasonic processing equipment has become more automated and intelligent.
For example, CNC technology now works with ultrasonic processing machines. This combination allows the machines to process efficiently and fully automatically. It reduces human error and improves production efficiency.
At the same time, the Internet of Things technology monitors the processing parameters. This helps ensure stable processing quality.
(4) Green manufacturing:
Ultrasonic machining technology reduces material waste and energy consumption. It does so because it uses low cutting force and operates with high efficiency. This aligns with the concept of green manufacturing.
In some applications, the project team optimized ultrasonic machining parameters. They aimed to reduce the environmental impact and promote sustainable development in the aerospace sector.
The inclusion of green concepts improves processing efficiency. It also helps reduce the environmental burden of the manufacturing process.
Table 1 Links and differences between advanced aerospace sheet metal fabrication technologies
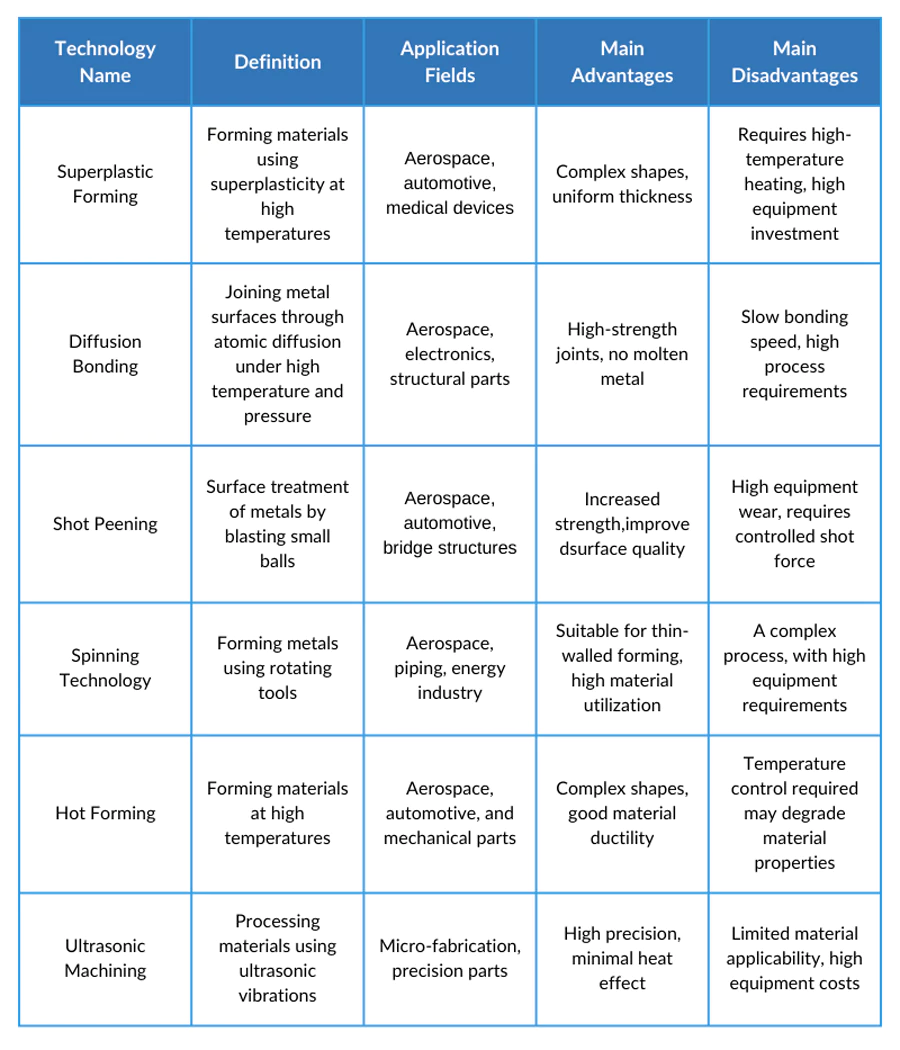
Conclusion
As the demand for high efficiency, long life, low cost, and high stealth in new military and civil aircraft increases, aviation manufacturing technology has experienced a comprehensive upgrade.
Aerospace sheet metal forming technology has made unprecedented progress. This progress is mainly reflected in several aspects:
First, the mature application of digital technology has significantly advanced the development of precise sheet metal forming technology. It has improved manufacturing accuracy and efficiency.
Second, the diversification of materials and the complexity of parts have led to the rise of new sheet metal forming technologies. These technologies meet the needs of complex designs.
Finally, solid basic research technology reserves have proven powerful at critical moments. They have provided strong support for technological innovation.