The quality and life of metal parts are largely influenced by their surface quality, and metal cutting machining is one of the key processes that affects surface quality.
With the continuous progress of CNC technology, the wide application of CNC machine tools has made the machining of complex parts more accurate.
Additionally, the use of computer-aided manufacturing (CAM) programming software has improved efficiency.
However, the characteristics of different parts require different machining processes, and vibratory cutting “plays” a crucial role in surface quality problems.
Therefore, a number of factors need to be taken into account during the machining of metal products.
First, the choice of material directly affects the difficulty of machining and product performance.
Secondly, structural rigidity, clamping rigidity and machine rigidity will affect the stability and accuracy of the machining process.
Tool selection is also critical, as different tools are suitable for different machining tasks.
Additionally, the cooling system can effectively control the temperature of the machining process.
This helps reduce the occurrence of cracks and stress concentrations, thereby extending the service life of the product.
Root fillet of the part appeared vibration knife and overcutting problem
In the field of manufacturing processes, the surface quality of the bottom fillet is a critical evaluation index.
However, in the case where the side walls are straight and the bottom is a free-form surface, the manufacturing process often encounters a series of problems.
In this case, the machined surface quality of the bottom fillet may not be satisfactory.
Experience has shown that when the sidewalls are straight and the bottom is free-form, the bottom fillet tends to have a number of problems.
Phenomena:
Firstly, it is common to observe wavy jagged marks on the surface of the bottom fillet.
These marks are closely related to vibrations and instabilities during machining.
Secondly, some crater marks may appear.
These may be caused by the unevenness of the material encountered by the tool during machining or by improper setting of the machining parameters.
In addition, signs of vibrating tools may be clearly visible on the sidewalls, which may be caused by unbalanced cutting forces or high cutting speeds.
The presence of these problems not only affects the aesthetic appearance of the bottom fillet.
More seriously, it may also affect its functional performance.
Cause Analysis:
In the problem of program toolpath, toolpath traces and vibration become critical.
Especially when dealing with free-form surfaces on the bottom side of the part, sidewall cutting and pit mapping are important factors to focus on.
Sudden changes in cutting force are also critical to consider.
It was observed that when the toolpath did not follow the root fillet cut, it often triggered a vibration phenomenon in the tool.
This occurred when the toolpath moved closer to or away from the sidewall.
In this case, the increase in the root fillet allowance even led to an increase in the cutting force, which further exacerbated the vibration.
In addition, when the radius of the tool fillet is the same as that of the root fillet of the part, the vibration increases.
This is due to the increase in the contact surface between the tool and the part.
It may even lead to the formation of small pits in the part as a result of the vibrating tool overcutting.
Therefore, to solve this problem, it is necessary to optimize the contact between the tool and the part.
This can be done by reducing the root fillet allowance and adjusting the tool fillet radius.
Additionally, planning a new program tool path will help reduce the vibration amplitude and ensure cutting quality.
Solution:
First of all, it is necessary to avoid frequent entry and exit of the tool at the rounded corners.
This will not only increase the machining time, but also lead to the deterioration of the surface quality of the workpiece.
Therefore, it is important to adopt a cutting strategy that follows the rounded corners.
This strategy not only improves machining efficiency, but also reduces vibrations caused by sudden changes in cutting forces.
This ensures stable and accurate machining, as shown in Figure 1.
Different machining processes are required for different types of bottom surfaces.
For a horizontal bottom surface, contour milling is ideal.
It can follow the rounded corners of the tool and effectively avoid unnecessary contact between the tool and the surface of the workpiece.
For free-form bottom surfaces, on the other hand, a three-step machining process is required:
First, there is finish milling of the sidewalls;
Then, it is finish milling the bottom surface;
Finally, it is finish milling rounded corners along the direction of rounded corner travel, i.e., root clearing operation.
In each step of machining, it is necessary to leave appropriate bottom surface allowance and side wall allowance.
This ensures that the bottom surface or side wall will not be milled and avoids milling to the rounded corner, thus ensuring machining quality and accuracy.
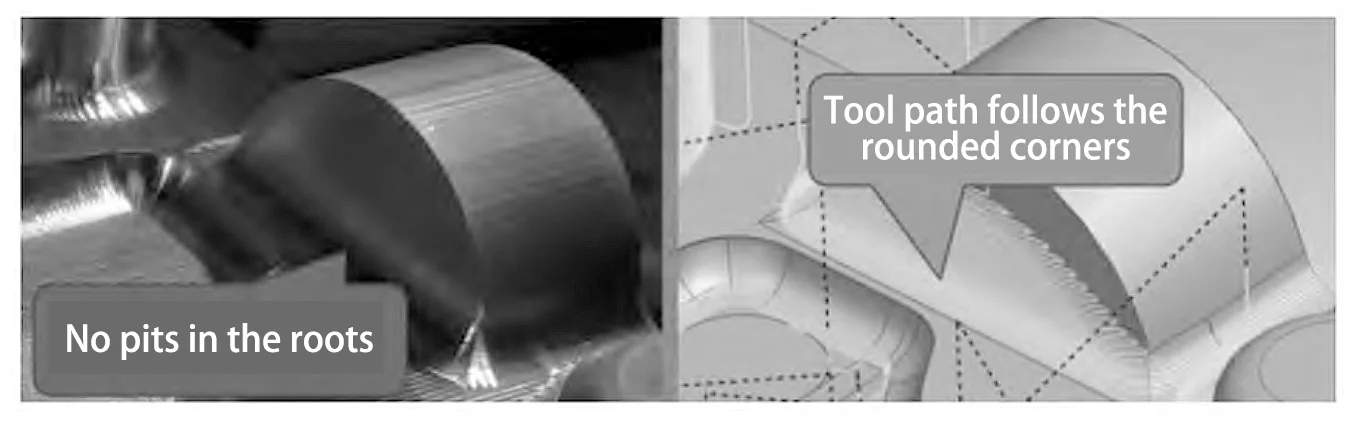
Root fillet of the horizontal bottom surface of the part occasionally appears one by one indentation of the problem
The root fillet of a part refers to the rounded transition where its sidewalls meet the bottom surface, and the bottom surface is in the shape of a horizontal plane.
Occasional dents appear when cleaning the root fillet, which may stem from factors such as improper setting of machining process parameters or tool wear.
These dents affect the appearance and quality of the part and, therefore, need to be recognized and resolved in a timely manner.
Improving machining process parameters and changing tools regularly are effective measures to prevent dents.
In addition, regular checking of equipment status and operating techniques is also critical to ensure accuracy and quality of part machining.
Therefore, for root fillet machining, in addition to technical means, operator experience and meticulousness are equally crucial.
Strengthening operator skill training and quality awareness education will help reduce the frequency of dents.
This, in turn, will improve the overall quality level of part machining.
Cause analysis:
CAM programming software has an automatic root-clearing function when processing models, however, this function has caused a series of problems.
Anomalies appeared in the design of the toolpath trajectory, and the Z-axis coordinates showed tiny fluctuations of about 2.1 microns.
To complicate matters, the machine’s axes had large backlash, especially in the Z-axis direction.
This caused the Z-axis to back off momentarily at the anomaly and then return immediately.
Although the small amount of Z-axis movement is smaller than the backlash, it is still enough to trigger Z-axis crosstalk.
This ultimately causes the tool to leave a dent in the workpiece surface.
So, while the Auto Clearance feature facilitates programming, one needs to be aware of the challenges that may be encountered in practice.
Adjusting the parameters or operation accordingly is necessary to ensure the quality of the final machining.
Solution:
First, the tolerance values of the CAM programming software can be adjusted to optimize parameters and reduce the impact of Z-axis fluctuations.
Second, explore alternative programming methods, such as planar milling with NX software, to reduce the need for the Z-axis and thus reduce the risk of fluctuations.
In addition to software adjustments, look at the machine itself, paying particular attention to Z-axis backlash.
If the backlash is small, machine parameters can be adjusted to compensate for this and offset the negative effect on machining quality;
If the clearance is too large, the machine must be repaired to ensure the stability and accuracy of the Z-axis.
Parts sidewall corners vibration knife and overcutting problems
Sidewall corner refers to the connection angle between the two sidewalls.
When the sidewalls are not vertical, it can cause surface quality problems, similar to root rounding caused by knife vibration and overcutting.
However, if the sidewalls are perpendicular, the situation may be quite different and may require separate treatment.
In this case, additional steps or special solutions may be required.
Therefore, when dealing with this type of problem, the angle of the sidewall and the associated chatter and overcut must be considered.
Particularly when dealing with vertical sidewalls, care should be taken to ensure that the treatment is effective in resolving surface quality issues.
Cause Analysis:
The tool is not matched to the corner radius and vibrates when cutting into the corner.
Vibration not only affects machining quality, but can also lead to tool damage or increased surface roughness of the machined part.
In addition, if the corner machining allowance is not controlled properly, excessive cutting force can occur.
This not only affects machining efficiency but may also damage the tool and machining equipment.
In addition, different materials and forms are required for different machining scenarios.
The choice of the appropriate tool material and edge form is also a key factor in improving cutting performance, while processing speed and tool high-frequency resonance affect stability.
Solution:
In the machining process, if the selection of tool radius is smaller than the corner radius of the workpiece, or if the corner radius is increased, it can effectively solve the problem of corner vibration cutter.
This adjustment makes the process smoother.
In addition, to reduce the machining allowance, first, roughing; then, finishing is the best practice.
Reducing the depth of cut to 0.2 mm per cut when setting the depth of cut can yield good results.
At the same time, the use of short tools or even custom-machined tools can improve machining efficiency and quality.
It is also important to enhance the strength and rigidity of the tool.
The use of high-strength, high-rigidity materials such as cemented carbide can help improve the quality and efficiency of machining.
Choosing unequal helical flutes or even considering vibration-resistant tools further enhances the machining performance.
When adjusting the machining speed, it is necessary to avoid the tool resonance frequency range.
Adjusting the speed effectively controls the vibration and resonance phenomenon, ensuring machining quality and safety.
Parts vertical sidewall vibration knife and overcutting problems
When dealing with vertical sidewalls, engineers are often faced with a trade-off between two different approaches.
A common approach is to use Z-layer milling, where the thickness of each cut is relatively large.
While this method is effective in improving machining efficiency, the surface quality tends to be rougher.
Another strategy is to cut the entire sidewall directly with the side edges of the machining tool.
Although this method results in a higher quality surface, it requires more careful control of the machining process to avoid possible surface quality problems.
In selecting an appropriate machining strategy, engineers must weigh the situation on a case-by-case basis.
If machining efficiency is a priority, especially for mass production, Z-layer milling may be more appropriate.
However, if surface quality is critical or precision machining is required, utilizing the side edges of the tool is more desirable, although it requires more careful process control.
Cause analysis:
Tool vibration is often a problem in tool machining, especially when machining root fillets and bottom surfaces.
This vibration not only affects the surface quality of the machined surfaces but can also lead to cuts on the sidewalls.
Setting the spindle speed parameter too high may be a major cause of tool vibration.
When the spindle speed is too high, the tool is prone to resonance.
This resonance increases tool vibration, which leads to instability in the cutting process and ultimately affects the machining quality.
Insufficient rigidity of the tool system is also an important reason for the vibration of the knife phenomenon.
The rigidity of the tool system includes the clamping extension length, tool material, tool edge form and other aspects.
If the rigidity of the tool system is insufficient, it is easy to lead to excessive vibration of the tool in the machining process, thus affecting the machining quality.
Solution:
A number of key factors need to be carefully considered when performing finishing operations, especially when dealing with sidewall and bottom surfaces.
Firstly, it is important to allow for adequate allowances and fillets, typically around 0.15 mm.
The purpose of this step is to avoid vibration of the tool during machining, especially when cutting into large root fillet allowances, which can lead to sidewall bruising.
When machining the bottom surface, it is necessary to allow for sidewall and fillet allowances.
This prevents the tool from hitting the sidewall of the part, which could potentially lead to sidewall cuts.
In addition, after finishing the sidewalls and bottom surfaces, the corner rounding is performed separately.
This step ensures that the vertical sidewall surfaces are smooth and meets the requirements for part surface quality.
In order to further improve the machining quality and efficiency, it is crucial to adjust the spindle speed.
By reducing the spindle speed, tool resonance can be effectively avoided, thus ensuring the stability and accuracy of machining.
In addition, it is also very important to improve the rigidity of the tool system.
Good rigidity of the tool system can effectively avoid vibration of the knife, which further improves the processing quality and efficiency.
Parts free-form surface bar-shaped pit overcutting problem
Free-form surface machining, commonly used ball nose tool or round nose tool for reciprocating line cutting.
These two tools can effectively shape complex surfaces, but they are also accompanied by some quality problems.
Surface roughness is one of the common ones, which may result from tool wear or inappropriate cutting parameters.
In addition, the appearance of prongs may be caused by tool vibration during machining or unstable cutting.
And irregular dents, similar to drawing streaks, are often caused by vibration or uneven cutting during machining, as shown in Figure 2, left.
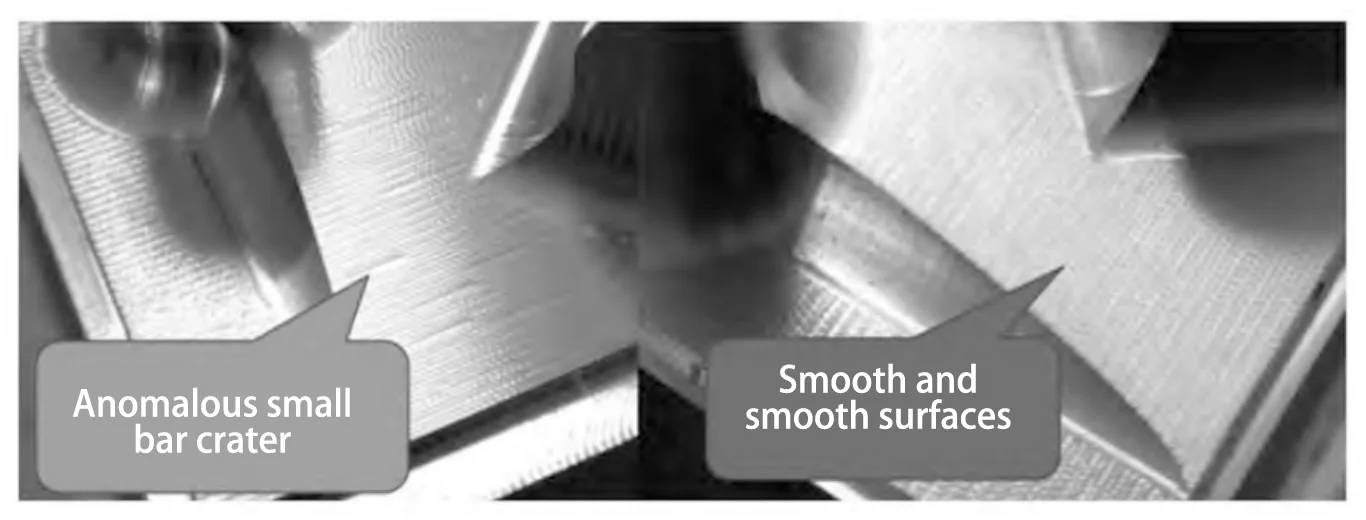
Solving these problems requires careful adjustment of machining parameters to ensure smooth cutting and timely replacement of badly worn tools.
In addition, surface design and mold manufacturing before machining are also critical, and quality problems can be reduced by optimizing the design and using high-precision molds.
Cause analysis:
During the programming process, a large number of anomalies occurred due to poor accuracy of the toolpath.
The machine crosstalk was affected by large gaps in the machine axes, especially in the z-axis direction.
In addition, poor machine parameters and poorly sharpened tools had a negative impact on the machine’s slag extrusion.
Solution:
To improve machining accuracy and surface quality, it is necessary to consider factors such as programming tolerance levels.
Additionally, tool path planning and machine parameter adjustments play a crucial role.
First, we increased the programming tolerance to ±0.003.
We also adopted a 45° toolpath strategy, which can effectively minimize small fluctuations in the toolpath and improve machining accuracy.
Next, we need to check the machine’s Z-axis backlash to make sure it is within normal limits.
If necessary, machine parameters can be compensated or repaired to ensure the stability and accuracy of machining precision.
In the machining process, it is crucial to use high-speed and high-precision machining instructions.
Conclusion
In summary, this paper combines a large number of practical proofs. In the process of CNC milling, a series of parts surface quality problems can arise.
By combining different processing methods corresponding to the parts and appropriately using a series of technical means, the processing quality of the parts can be further improved.
This ultimately enhances the core competitiveness of enterprises.