With the continuous development of the modern manufacturing industry, laser cutting technology has become increasingly prominent.
This is especially true in the field of sheet metal manufacturing, where it has seen a large number of applications.
Therefore, the manufacturing industry and technical personnel must be clear about the basic situation of laser cutting technology and its main types.
Then, based on this understanding, they should combine it with the actual manufacturing materials, and apply the corresponding laser cutting technology in a reasonable way.
laser cutting technology can fully exploit its technical advantages.
It can meet the actual production and processing needs of the manufacturing industry.
It also promotes the use of laser cutting technology. Additionally, it contributes to the synergistic development of the modern manufacturing industry.

Overview of laser cutting technology
1. Basic introduction
Laser cutting technology involves using high-power density laser beam irradiation to cut material, which rapidly vaporizes, ablates, melts, or reaches the ignition point, evaporating to form tiny holes.
At the same time, with the help of the laser beam coaxial auxiliary high-pressure gas, the molten material will be blown off.
As the laser beam moves, the hole continuously forms a narrow-width slit, thus completing the cutting of the processed material.
The basic application principle of laser cutting technology is shown in Figure 1.
The main advantages of this technology include good cutting quality, high cutting efficiency, fast cutting speed, no need to contact the processed material, and strong applicability.
Modern manufacturers widely use laser cutting technology because of its advantages.
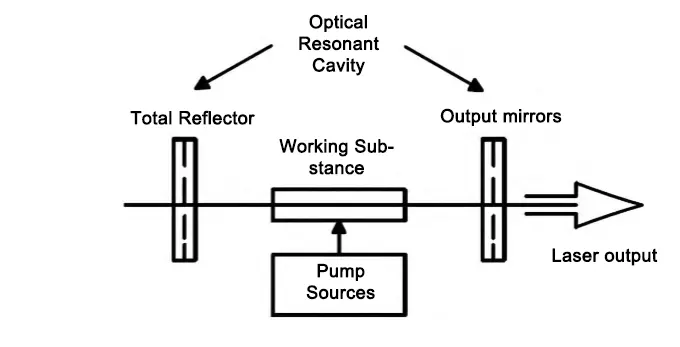
2. Application Status
Manufacturers widely use laser cutting technology in today’s industry, especially in mechanical production, because it is highly adaptable and can cut and process a variety of materials.
From the point of view of cutting materials, laser cutting technology has three main application directions:
One is for cutting metal materials. Two are for cutting non-metallic materials. Three are for cutting other materials.
No matter in what kind of material cutting processing, laser cutting technology has shown very significant application advantages.
Therefore, the development prospects of laser cutting technology are also very broad in the modern manufacturing industry.
Main types of laser cutting technology
1. Vaporization cutting technology
Manufacturers most widely use vaporization cutting technology in laser cutting applications.
When the technology applies high power density laser beam irradiation to the surface of the material to be cut,
A small amount of the laser will be reflected. Most of the laser will be absorbed by the laser cutting surface.
The surface temperature of the cut material will quickly reach its boiling point, which leads to the vaporization of the cutting part of the material.
This process results in the formation of small holes.
At the same time, under the influence of surface oxidation, etc., the ejected steam will carry away most of the molten material and ultimately form a very narrow vaporization incision on the cutting surface.
This technology is usually realized with the help of a pulsed laser, and its main application is the cutting of wood, ceramics, plastics, and other non-melting materials.
2. Melting cutting technology
Melting cutting is also a type of laser cutting technology. In specific applications, this technology requires relatively high laser power requirements.
Compared with vaporization cutting technology, this method removes the melted material not through vaporization but by using auxiliary gas to blow it away.
With this cutting technique, the laser beam is not affected by vapor during the cutting process, and it only interacts with the material in front of it when moving in the kerf gap.
In addition, the laser power density used in this cutting mode is relatively small.
The laser beam will form a sizeable beveled shooting angle on the transmission surface of the material during cutting.
This results in the cutting surface not absorbing enough laser energy to meet the needs for continuous melting.
Therefore, the melting process should be carried out gradually. The final cutting will form a wave-shaped pattern.
This cutting technology is very suitable for cutting materials that can have an exothermic reaction with oxygen, such as copper and aluminum.
In the blowing off of the melted material, the commonly used auxiliary gases are mainly inert gases of various types.
3. Reaction melting cutting technology
Reaction melting cutting uses a laser beam to heat the surface of the cut material or workpiece.
This heating raises the surface temperature to the ignition point. Then, industrial pure oxygen is applied to react with the processed material, releasing a large amount of heat.
Ultimately, this process forms a molten oxide at the position of the seam.
When blowing off these molten oxides by means of auxiliary gases, some of the heat will be absorbed by the neighboring materials, gradually increasing their temperature.
When the temperature reaches the ignition point, a combustion reaction will also take place, further releasing more heat.
In this way, the reaction-melting cutting process can continue continuously.
Compared with the first two laser cutting technologies, this cutting technology applies laser power density lower, usually only 1/20 of the vaporization cutting technology.
In the current machinery manufacturing field, this laser cutting technology is mainly used for cutting materials such as titanium and steel.
Specific applications
With the application and development of laser cutting technology, this technology has an increasingly wide range of applications in the modern manufacturing industry.
It also reflects increasingly significant application advantages. Currently, the laser cutting technology in the manufacturing industry in the main application direction is as follows.
1. Metal material processing
In the modern manufacturing industry, metal material processing can significantly improve its efficiency.
It can also reduce processing costs through the reasonable application of laser cutting technology.
This can also further improve the processing accuracy of metal materials, resulting in more precise products.
However, due to the technology’s limitations, it is only applicable to the cutting and processing of sheet metal and is not applicable to the processing of thick sheet metal.
Regarding the current manufacturing cutting processing plant, carbon dioxide laser is the most commonly used laser cutting equipment.
Its 2 kW output power allows it to quickly cut 8 mm below the thickness of stainless steel and 12 mm below the thickness of ordinary carbon steel.
This technology and equipment can significantly improve the efficiency of manufacturing metal material cutting and processing by being reasonably applied.
Additionally, it helps reduce material loss in processing and results in higher-quality processed products.
Compared with traditional cutting and processing technology, laser cutting technology produces and processes finished materials more in line with the design standards.
Under normal circumstances, its positioning accuracy can be controlled at 0.05 mm, and its repeat positioning accuracy at 0.02 mm.
Therefore, with the continuous development of the manufacturing industry, the
Therefore, with the continuous development of the manufacturing industry, the application of laser cutting technology in the field of metal materials processing is becoming increasingly extensive.
It is gradually becoming one of the important processes in modern manufacturing.
This will also further promote the manufacturing industry to high-end, digital, and intelligent transformation and development.
2. Non-metallic material processing
In addition to being more applicable in the manufacturing industry for processing metal materials, laser cutting technology is also very good at processing non-metallic materials.
In the current manufacturing field, laser cutting technology can be used to process synthetic non-metallic materials and organic non-metallic materials, such as cutting.
Compared with metal materials, non-metallic materials have a higher absorption rate of lasers.
Therefore, when laser cutting technology is applied to the cutting and processing process, it will achieve higher production and processing efficiency than when used with metal materials.
Therefore, laser cutting technology is also widely used in non-mechanical product cutting processing, such as processing watch gemstones on the shaft hole, non-metallic template processing, and so on.
In the laser cutting process of these materials, the processing gases used for different non-metallic materials are also different. Non-metallic materials and cutting parameters for laser cutting are shown in Table 1.

Laser cutting technology in non-metallic materials can be effectively applied by reasonable control of the above processing parameters.
This approach ensures the processing efficiency and accuracy as much as possible, producing higher-quality products.
Additionally, it helps realize overall production and processing cost control.
It is the only way to ensure that laser cutting technology is well applied in the processing of non-metallic materials.
3. Mechanical mold processing
Laser cutting technology in machinery mold production and manufacturing is mainly reflected in two major directions.
The first direction is its use in producing stacked molds made of steel.
The second direction is its application in forming thin plate-stacked three-dimensional molds.
For steel plate system stacked mold cutting processing, the staff can follow the model design standards.
Using laser cutting technology, they can perform high-precision cutting on steel plates with a thickness of no more than 6 mm.
This ensures the completion of the entire stacked mold production and processing.
After practical application, it is found that this technology’s economic cost in the manufacturing of steel plate laminated molds is only about 1/3 of that of the ordinary mechanical processing mode, which has good economic benefits.
At the same time, the molds processed by this technology also have very high precision; their accuracy can generally be controlled at ± 0.01 mm.
For thin plate stacked into a three-dimensional mold, laser cutting, the operator can use computer-aided design (CAD), computer-aided manufacturing (CAM) and other software combination of processing.
This method effectively ensures the production and processing accuracy of such mechanical molds and reasonably simplifies their design and manufacturing process, resulting in higher production and processing efficiency.
Direction of development
Although laser cutting technology has been widely used in the modern manufacturing industry and offers significant application advantages, the industry’s development continues to progress.
As production and processing technology requirements improve, the application of laser cutting technology also needs further development.
Through the practical application of laser cutting technology in the current manufacturing industry, certain shortcomings have been identified.
One such limitation is the restriction on material thickness.
Laser cutting technology cannot effectively cut and process materials with larger thicknesses.
Laser cutting equipment has a high cost, making it unaffordable for some small and medium-sized manufacturing enterprises.
As a result, its promotion effect is not ideal.
Additionally, laser cutting technology has not yet established an effective link with many current advanced technologies.
Furthermore, the overall operation and control of this technology still have significant room for improvement.
Based on this, in the future development of the manufacturing industry, laser cutting technology should be developed in the following directions:
(1) to take reasonable methods and measures to improve the laser cutting ability continuously so that it is more adaptable in the thickness of the material, so as to expand its scope of application constantly;
(2) the cost of laser cutting equipment can be effectively reduced through reasonable technical improvements.
Supporting hardware and software enhancements play a crucial role in achieving this cost reduction.
By lowering costs, laser cutting technology can be widely adopted by more manufacturing enterprises.
This will ultimately lead to a more ideal application and promotion effect.
(3) Modern big data technology, automation technology, and intelligent technology should be integrated into laser cutting technology in practice.
Based on this integration, corresponding information technology, automation, and intelligent laser cutting control systems can be developed.
This approach will enhance the level of information technology, automation, and intelligent control in laser cutting.
As a result, it will maximize control effectiveness, processing efficiency, and product quality.
In this way, we can make laser cutting technology in the modern manufacturing industry to play a better application advantages, and with the modern manufacturing industry, towards a more advanced direction.
Conclusion
In today’s manufacturing industry, laser cutting technology has significant advantages for application.
Based on this, relevant enterprises, researchers, and staff must strengthen the study of laser cutting technology.
They should understand its basic principles, main functions, and current applications.
By considering the actual production and processing needs of modern manufacturing, they can reasonably introduce laser cutting technology.
At the same time, it should be based on the manufacturing industry’s future development goals to take a reasonable approach to the innovation of laser cutting technology so that it moves in a better direction.
In this way, laser cutting technology will have better application advantages in the manufacturing field.
It can meet the actual production and processing requirements for various materials and workpieces in the manufacturing industry.
This enables the synergistic and sustainable development of laser cutting technology and modern manufacturing.
FAQ:
Laser cutting technology uses a high-power density laser beam to heat materials to their melting, vaporization, or ignition point. It then uses auxiliary gases to blow away molten material, forming a narrow slit and completing the cut.
The three main types are:
Vaporization cutting: Material is vaporized using a high-power laser.
Melting cutting: Uses laser and gas to melt and blow away material.
Reaction melting cutting: Involves combustion with oxygen to assist cutting.
Laser cutting is suitable for a wide range of materials, including:
Metal materials like carbon steel, stainless steel, titanium
Non-metallic materials such as ceramics, plastics, wood, and synthetic materials
Specialty materials used in mechanical molds and watch components
High cutting precision
Clean and narrow cuts
Minimal material waste
No physical contact with the workpiece
Fast processing speeds
Strong adaptability to different materials
Difficulty cutting thick materials
High initial equipment cost
Limited accessibility for small to medium-sized businesses
Need for better integration with modern automation and control systems
Sheet metal fabrication
Mechanical manufacturing
Mold making
Watch and precision part industries
Automotive and aerospace sectors
The gases vary based on material and technique:
Oxygen for reaction melting (oxidation cutting)
Inert gases (like nitrogen or argon) for melting and vaporization cutting
Specific gases are selected to aid cutting and reduce oxidation or contamination.
Non-metal materials absorb laser energy better, leading to:
Higher cutting efficiency
Greater precision
Lower thermal distortion
Wider application in non-mechanical industries
Laser cutting allows high-precision shaping of laminated steel molds and 3D thin-plate molds. It reduces production costs and improves accuracy to ±0.01 mm, especially when combined with CAD/CAM software.
Improving cutting capacity for thicker materials
Lowering equipment costs for broader accessibility
Integrating with automation, big data, and intelligent control systems
Enhancing control, efficiency, and product quality in smart manufacturing