Manufacturing systems consist of multiple complex chains that interact with each other. Decisions made in one chain can have a ripple effect on the other chains. Integrating DFM into the decision-making process can help simplify design and improve efficiency.
For example, material selection affects product performance, manufacturing process, equipment, raw material supply, and cost.
The core issue of modern manufacturing technology is how to consider all aspects together to achieve global optimization.
Problems and challenges of the traditional manufacturing model
In conventional manufacturing systems, different departments handle each section, focusing on their needs without considering other links.
This kind of separate management leads to poor communication, frequent conflicts between upstream and downstream chains, a lot of rework, resource waste, and difficulty achieving global optimization, which restricts enterprises’ efficiency and effectiveness.
Especially in the disconnect between design and manufacturing, designers focus on functional design, while the manufacturing process is the responsibility of engineers.
The “throw-over-the-wall” design model causes frequent rework, processing difficulties, low efficiency, and rising costs.
These issues become even more prominent in the face of fierce global competition.
To boost competitiveness, manufacturers must rethink the design process, adopt Design for Manufacturing (DFM), improve product quality, reduce costs, and respond quickly to market demands.
Concept of DFM
DFM, Design for Manufacturing, is a methodology that incorporates manufacturing feasibility and economic considerations in the product design phase.
Its core idea is to optimize the manufacturing process, reduce costs, and achieve efficient production while meeting functional and performance requirements.
Manufacturability is the crucial goal of DFM, which means that the design should meet the technical requirements and facilitate the actual manufacturing.
1. Advantages of DFM
Adopting the DFM design methodology considers both design and process simultaneously, offering the following significant advantages:
(1) Early detection of problems and reduced rework:
The design can expose potential process problems early, preventing rework.
(2)Optimize costs and improve competitiveness:
Evaluating the manufacturability of different design options helps select the one with the lowest processing costs, significantly reducing production costs.
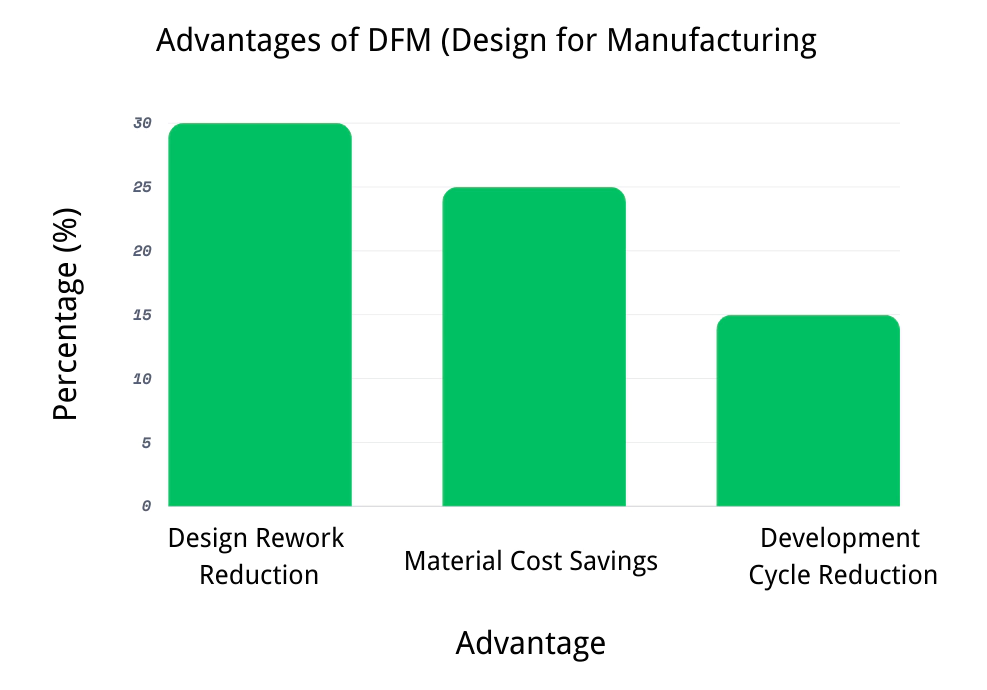
Research shows that although the design process accounts for a small portion of product costs, the design phase determines 70%-80%, while the manufacturing phase accounts for only 20%-30%.
Therefore, improving the quality and efficiency of design is critical to reducing overall costs and improving an organization’s competitiveness.
2. Case Illustration: Optimized Design of Automotive Components
An automotive manufacturer used a traditional approach to designing engine mounts, with designers focusing on functionality and performance without considering manufacturing difficulties.
As a result, during the production phase, due to the complexity of the bracket design, frequent rework occurred during machining, leading to a significant increase in time and cost.
With the introduction of the DFM methodology, the design team worked with the manufacturing engineers during the design phase to simplify the bracket’s shape and optimize it for machining on CNC machines.
This dramatically reduced machining time and saved approximately 20% in material costs.
In addition, the simplified design reduced machining errors by 30%, further improving product quality.
Ultimately, this improvement helped the company significantly reduce production costs in a highly competitive market while speeding up time-to-market.
3. The combined value of DFM
Although the introduction of DFM may increase the time and cost of the design phase, this investment can be compensated in the subsequent processing and assembly phases.
For example, in the above case, the improved design reduces unnecessary corrections and coordination in the manufacturing phase, shortening the development cycle and reducing production costs.
Through DFM, enterprises can optimize product design and achieve the goals of high quality, low cost, and fast response to market demand, significantly enhancing market competitiveness.
Table 1 Comparison of benefits between DFM and traditional design methods
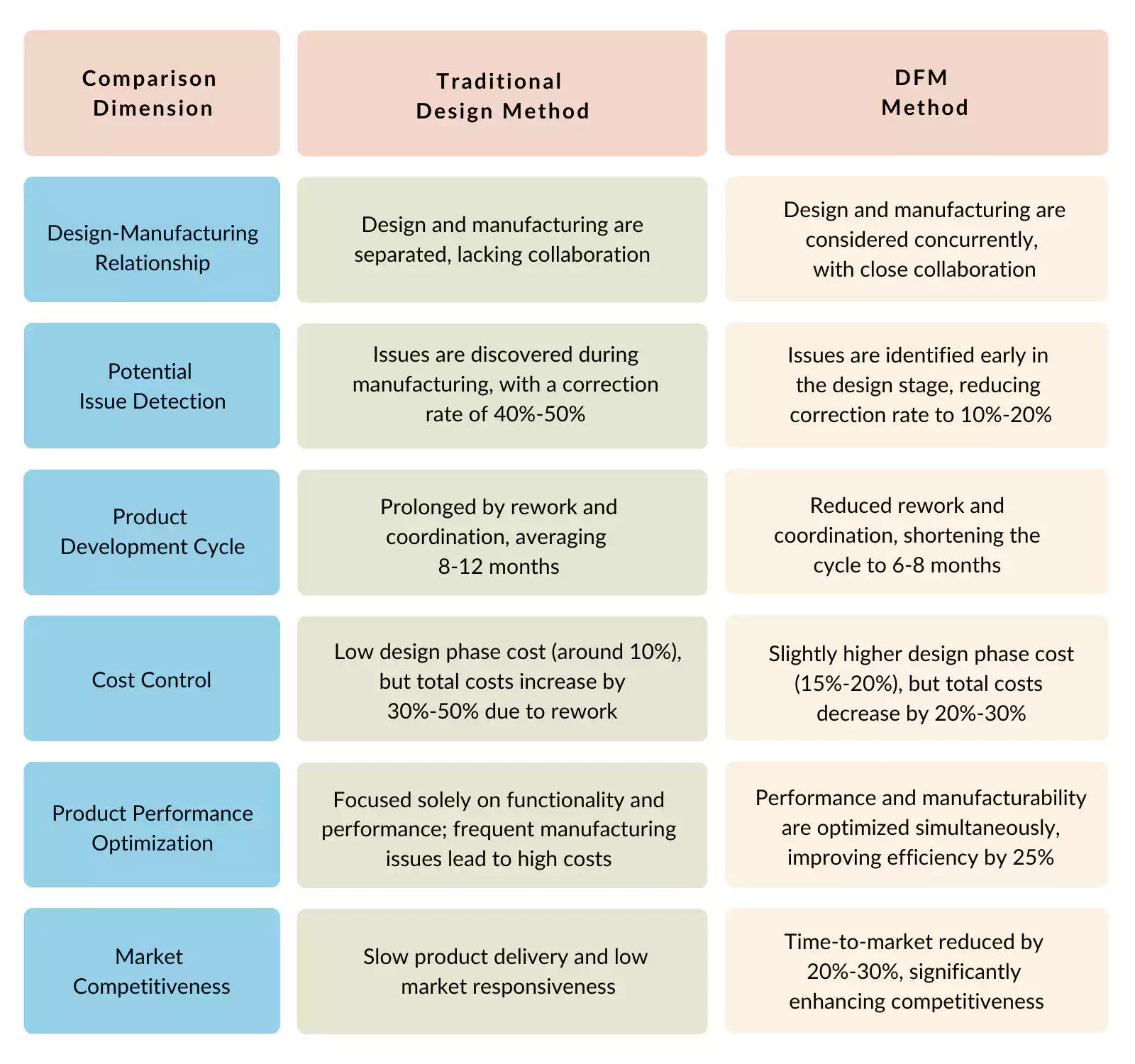
DFM Methodology
Since the 1970s, engineers have realized the importance of considering the manufacturing process when designing.
Many design methods reflecting DFM ideas have emerged, most of which are qualitative guidelines that play an essential role in actual design.
1. Axiomatic Approach
DFM emphasizes that good design follows specific principles or axioms, guiding design decisions to ensure manufacturability.
In 1977, scholars summarized two basic axioms by analyzing good designs:
(1) The features and components of the design should independently fulfill each functional requirement.
(2) A good design should realize the function with minimum complexity, simplify the design, and reduce the amount of information.
Although these axioms are abstract, engineers with extensive experience can better apply these guidelines.
2. DFM Guidelines
DFM Guidelines are specific rules based on many years of design and manufacturing experience that help a design maintain good manufacturability while utilizing the designer’s creativity. Typical guidelines include:
(1) Reduce the number of parts
(2) Reduce the variety of parts
(3) Use standard parts wherever possible
(4) Design similar features to uniform dimensions
(5) Optimize the machining surface. Choose the outer surface machining instead of the inner surface machining.
3. Process-driven Design
The process-driven design ensures that the designed parts and products can be manufactured using a specific process.
The process typically communicates its requirements through design guidelines.
These guidelines are often specialized for a particular plant, process, or type of machining equipment.
The key to DFM is to provide designers with a clear understanding of process requirements and constraints early in the design phase, ensuring that the final design aligns with the process.
Process-driven design falls into two categories: process-specific design and equipment-specific design.
DFM for the process ensures that the design requirements of parts are suited for a specific manufacturing process, such as casting, forging, or stamping.
Casting, forging, and stamping-oriented designs all fall into this category.
Equipment-specific DFM designs products that will be processed on a particular piece of equipment. Some typical application environments include.
Some typical application environments include flexible assembly and manufacturing systems, unique flexible welding fixtures or production lines, etc.
4. Group Technology Auxiliary DFM
Group Technology (GT) is a design and manufacturing method.
It reduces the amount of information in the manufacturing system by recognizing the similarity of parts in shape and process.
The method supports product design, manufacturing, and management.
When design engineers use the GT system as an aid to DFM, they first determine the part’s group code based on functional requirements.
Then, similar parts are found by searching the GT parts database.
Finally, these parts are modified according to the new requirements to obtain a new design.
As long as the excellent manufacturability of the parts already in the database is ensured, the manufacturability of the new design is guaranteed.
More importantly, grouping technology can effectively control the multiplication of part types and reduce redundant new designs.
This reflects the product standardization and serialization of design ideas so that the enterprise’s parts types form a system.
New designs are grouped into existing part types as much as possible, which is conducive to improving design efficiency and is easy to manage.
More importantly, process standardization and serialization can reduce product manufacturing costs and shorten the production cycle, indirectly improving manufacturability.
5. Implementation Barriers
Despite the many advantages of the DFM methodology, some barriers still exist to its practical application.
(1) Cross-disciplinary knowledge requirements
DFM requires designers to comprehensively understand design skills, process knowledge, and corporate resources.
Existing designers usually focus on design theories and tools (e.g., finite element analysis and 3D modeling) and lack an in-depth understanding of process selection and cost estimation.
(2) Challenges of Collaborative Workgroups
DFM emphasizes cross-functional teamwork, and design, process, and tooling department members should work together.
However, a company’s organizational structure often becomes an obstacle to cross-functional collaboration.
It is difficult to realize in practice the efficient operation of temporary teams, which results in poor information communication and reduced synergy effects.
Computer-aided DFM method
Since the introduction of DFM in the 1970s, its implementation has been limited due to various difficulties in traditional design environments.
However, with the rapid development of computer and communication technologies in the 1980s, DFM has been given a real opportunity for development.
Here are the top three enablers of computer-aided DFM (CAD + DFM):
1. Artificial Intelligence and Expert Systems
Advances in artificial intelligence and expert systems have made it possible to have a “total designer” who understands both design and process.
DFM expert systems, built on computer-aided design (CAD) systems, can assess a design’s manufacturability, help designers identify problems early on, and suggest modifications.
Features:
The expert system integrates process knowledge base and resource data (e.g., machine tools).
Provides online or staged evaluations based on different design phases.
Evaluation results include recommendations for design improvements.
2. Computer Networks and Communication Technologies
The development of computer networks has enabled design and process departments to communicate efficiently over the network and promptly identify potential problems in design.
This promotes close collaboration between design and manufacturing and avoids the problems of information lag and miscommunication.
Advantage:
Departments can communicate easily through the network and solve problems more quickly.
Collaboration between design and process is more seamless.
3. Powerful Computing
The power of computers allows designers to quickly evaluate multiple design options and conduct “what if” simulations to optimize the design.
This way, designers can filter out the most suitable solutions early in the design process, improving decision-making efficiency.
Forms of computer-aided DFM systems
There are various forms of computer-aided DFM systems, including the following main methods:
1. knowledge-based manufacturability evaluation system (DFM expert system)
This system evaluates the manufacturability of CAD designs through a knowledge base and resource data. It evaluates the strengths and weaknesses of different design alternatives and predicts manufacturing costs and production time.
Advantages:
The DFM system remains self-contained and easily modularized.
Provides effective manufacturing cost and time estimates.
Challenges:
During the design phase (especially early on), design information is often incomplete and lacks process information, making it difficult to evaluate accurately.
2. CAD/CAPP Parallel Interactive Design System
This system integrates CAD with computer-aided process design (CAPP) to synchronize design and process.
By exchanging information in real time over a network, manufacturing problems in design can be instantly fed back to the CAD department.
Advantages:
The system supports parallel design, completing product and process design almost simultaneously.
CAPP support eases DFM.
Challenges:
It requires a powerful computer communication system and database management.
Parallel design may lead to longer design phase time, and complex process control increases the system’s burden.
3. Design for Manufacturing (DFM) system
Unlike the previous two approaches, this approach incorporates DFM elements directly into the CAD system by creating a library of feature elements based on specific process types (e.g., casting, forging, cutting, etc.) and manufacturing resources.
The designer models using the feature elements in the library, ensuring that the part is well-manufacturable.
Benefits:
Direct constraints on the part design process reduce the need for feedback for after-the-fact evaluation.
Simple interaction between CAD and CAPP avoids the complexity of feature extraction.
Challenges:
The limited feature library size makes it difficult to model complex structures.
Design flexibility is limited, and designers must translate design intent into appropriate manufacturing features.
Computer-aided DFM is an integral part of modern design and manufacturing.
It integrates the design and manufacturing process, utilizing advanced computer technology.
This helps designers evaluate and optimize designs more efficiently and reduce costs.
Ultimately, it can shorten development cycles and improve product manufacturability and market competitiveness.
Although existing CAD systems have their limitations, especially regarding active decision support.
However, as technology advances, computer-aided DFM is becoming a mainstream trend in the industry.
Through continuous optimization of system functionality and cross-functional collaboration, DFM will help companies compete globally.
4. Diagram: Computer-Aided DFM Flowchart
The following is a simplified illustration of the computer-aided DFM workflow:
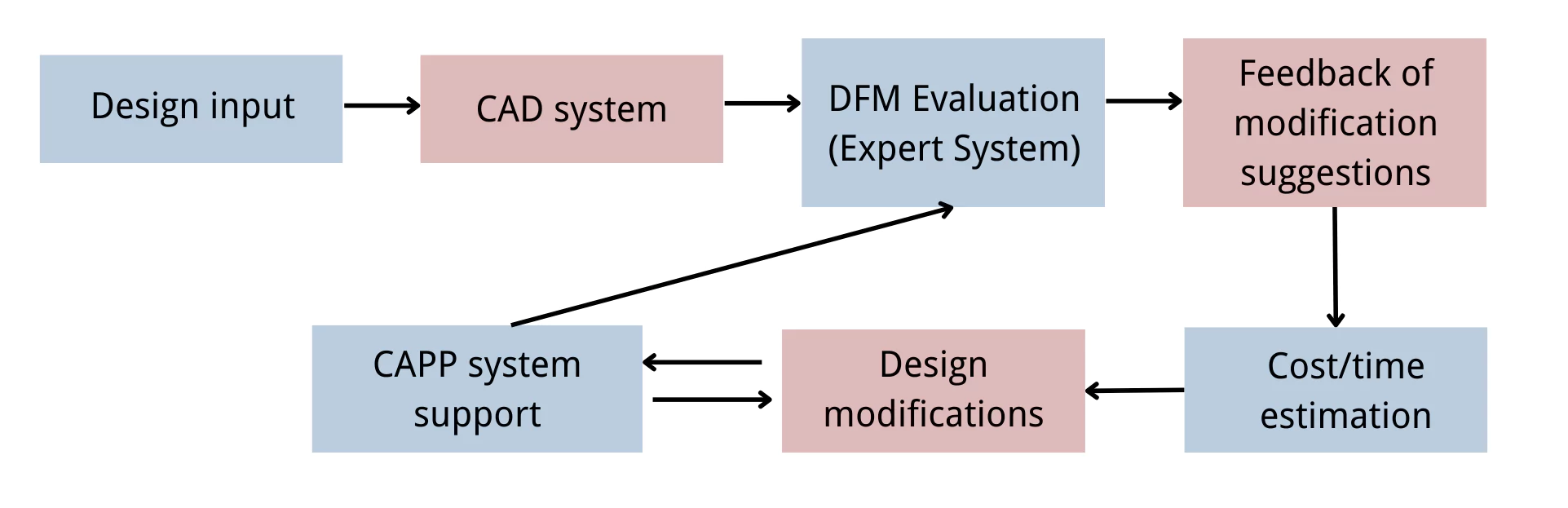
(1) Design Input: Preliminary design requirements for the product.
(2) CAD System: Complete geometric design and fundamental analysis.
(3) DFM Evaluation: Evaluate the design based on the manufacturability knowledge base and recommend changes.
(4) CAPP System: Provides process design and manufacturability feedback.
(5) Feedback Modification Recommendations: Based on the evaluation results, the design is adjusted to meet manufacturability requirements.
(6) Cost/Time Estimation: Predicts manufacturing cost and time to inform decision-making.
Through this process, designers can complete designs more efficiently and ensure that manufacturability and productivity are maximized.
Content and architecture of DFM
1. Types of DFM
DFM (Design for Manufacturing) is design optimization for improving product manufacturability and reducing costs. It is categorized into two types: broad and narrow.
(1) Broad DFM:
Including assembly-oriented design (DFA) and processing-oriented design (DFF).
DFA focuses on simplifying product structure and improving assemblability by reducing the number of parts.
DFF focuses on part structure and machining economics, optimizing parts to fit existing manufacturing resources.
(2) Narrow DFM:
It focuses on design for parts (DFF), parallel to DFA, and emphasizes feasibility in the manufacturing process.
2. Three core issues of the DFM system
(1) Structural manufacturability issues (independent of resources)
The DFM system evaluates part geometry and accuracy to determine its machinability.
Designs that cannot be machined conventionally, e.g., surfaces inaccessible to the tool or parts with sharp corners.
Designs that are difficult to machine, such as thin-walled parts or complex holes.
(2) Manufacturability Issues (Resource Related)
Analyze whether the part can be produced with available resources.
Evaluate whether accuracy requirements are beyond the machine tool’s machining capability.
Check whether suitable tools are available to machine the holes in the part.
(3) Manufacturing Economy Issues
The DFM system provides estimates of manufacturing costs and machining times to help designers optimize their designs.
The machining cost and time of the part are estimated by mathematical modeling.
3. Relationship between DFM and CAD and CAPP systems
DFM is closely integrated with CAD (Computer-Aided Design) and CAPP (Computer-Aided Process Planning) systems.
These three need to integrate information and functions and work together.
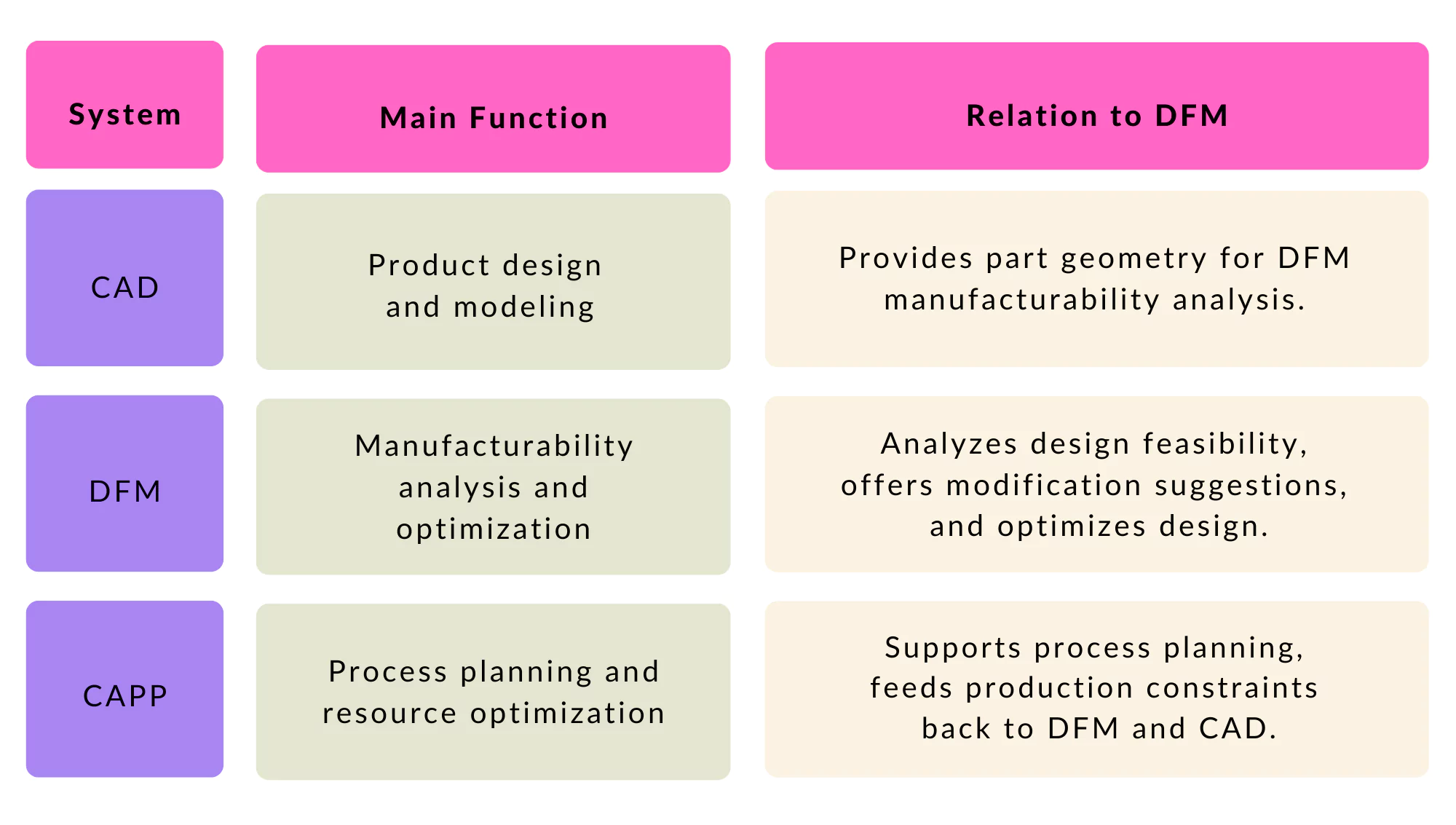
DFM is a key method of ensuring that designs are easy to manufacture, reduce costs, and increase efficiency.
By focusing on the part’s structure, resource requirement, t,s, and economics, designers can better optimize the product design and manufacturing process.
By tightly integrating with CAD and CAPP systems, DFM ensures that design, process, and production are seamlessly integrated, thereby increasing products’ competitiveness in the marketplace.
Conclusion
The need for high quality, low cost, and fast response times has made DFM (Design for Manufacturing) a key design concept.
However, the traditional DFM approach is more of a theoretical guide, and only by combining computer technology can DFM truly realize its potential and application value.
The theoretical model of the computer-aided DFM system is not yet fully mature, and the research methodology also needs to be improved.
This requires in-depth exploration and improvement in practical application. An in-depth study of DFM technology will strongly support enhancing the competitiveness of the manufacturing industry and is of great strategic significance.
At Ruiyi, we utilize experienced engineers and computer-aided DFM systems to serve our customers and meet their requirements for product quality and cost.