CNC technology is an important foundation and key technology for the modernization of the manufacturing industry. CNC machining solves complex, precise, and small-batch part machining issues. It stabilizes quality, shortens processing time, and boosts production flexibility. This improves efficiency, accelerates product development, and enhances the company’s market adaptability and economic benefits.
Product quality is key to a company’s competitiveness and economic benefits. Process quality is the foundation of product quality. The core of quality control in manufacturing is machining process control. Studying CNC machining quality control is crucial for enhancing a company’s core competitiveness.
This paper explores the transition from traditional to CNC equipment in manufacturing. It examines CNC machining software and hardware. The study focuses on CNC machining quality control in digital manufacturing, aiming to identify key elements for efficient control.
CNC machining process quality control system structure
1. The current situation and problems of quality control system structure
Years ago, a few forward-thinking companies shifted from traditional machining to CNC manufacturing as part of their development strategy.
Industries need higher efficiency and accuracy, driving the replacement of traditional lathes, mills, and drills with CNC machines.
However, in the transition process, in the quality control of the CNC machining process, there are the following problems:
(1) The traditional process flow limits the stability of part quality
The conventional process flow mainly arranges ordinary machine tool machining, with scattered work processes and more parts turnover links.
Repeated positioning and clamping many times lead to large deformation of parts, making shape and position tolerances difficult to ensure. This makes part quality unstable.
(2) Rough preparation of process programs traditional process program overlooks the use of new cutting tools, and efficient cutting parameters lack practical verification.
Workers process parts based on experience, which significantly affects processing quality.
Their operating skills influence the actual processing efficiency, resulting in low efficiency and many hidden quality problems.
(3) Insufficient process technology support
Too few process technicians exist, and their skills vary, leading to unstable quality in new product processes.
The CNC machining process card is too basic and lacks essential information, hindering efficient production guidance.
CNC programming efficiency is low, and tool, jig, cutting tool, and gauge preparation take too long, reducing machine efficiency.
(4) quality control methods and tools application is missing
Advanced quality control methods and tools in the CNC machining process are insufficient.
Has not yet established a quality control model for the CNC machining process applicable to specialized production workshops.
The lack of quality control tools limits part processing quality and CNC machine efficiency, affecting production success.
2. CNC machining process operation flow model
Figure 1 shows the old process model for most of the company’s CNC machining operations.
By applying process quality control, CNC machining quality reflects how well the results align with design, technology, and production requirements.
We track process indicators like delivery pass rate, scrap rate, rework rate, quality loss, production adherence, and on-time delivery.

Figure 1 CNC machining process operation flow model
CNC machining quality control limits process fluctuations within required boundaries.
The process indicators at the output point reflect the key aspects of process control.
The six key factors closely related to quality control can be identified from the CNC machining process steps in Figure 1.
(1) Machine
The stability, accuracy,y, and reliability of CNC machine tools directly affect the processing quality.
Maintenance of equipment, maintenance, and timely troubleshooting are particularly important.
(2) personnel (Man)
The operating workers’ skill level and quality consciousness affect the processing results.
Improve staff skills training and strengthen quality management awareness.
(3) Method
The scientific nature of the process program and processing strategy.
Optimize process design, reasonably prepare CNC programs, and adopt advanced machining methods.
(4) Information
Information transfer and feedback related to CNC machining.
Ensure the CNC machining process documents, operating procedures, and process parameters are accurate.
(5) Material
The quality of raw materials has a significant impact on the quality of parts processing.
Strengthen material testing and supply chain management to ensure that raw materials meet the processing requirements.
(6) Measurement
The precision of testing equipment and the scientific nature of testing methods.
Equipped with advanced measuring tools and improve the testing process to ensure that the machined parts meet the design requirements.
3. CNC machining process quality control system structure
The quality control system of CNC machining includes key steps to ensure the process meets design, technology, and production quality requirements.
(1) Quality Planning
Quality planning is the starting point of the quality control of the CNC machining process. Translate the design, process, and production requirements into specific CNC machining quality characteristics.
These characteristics define CNC machining quality and set standards for future quality control.
(2) Formation of quality control objectives
We determine the quality control objectives for key processes based on the identified quality characteristics.
These objectives set the quality standards for each key process and guide quality control.
(3) Decomposition of quality control specifications and process parameters
We decompose the quality control objectives of key processes into specific quality control specifications and process control parameters.
These specifications ensure detailed monitoring and quality control at each stage.
(4) Real-time quality data collection and measurement
During dynamic CNC machining, the system collects real-time data on production quality.
Modern sensors and measuring equipment ensure timely monitoring of part quality and process parameters to meet machining requirements.
(5) Quality statistical analysis and control
We use statistical analysis tools (e.g., SPC) and control methods (e.g., feedback control) to compare actual data with quality control objectives of key processes.
This allows us to assess the quality status of the processing in real-time and identify potential quality problems.
(6) Quality evaluation and decision-making
We evaluate quality based on statistical analysis to determine the current production process’s quality level.
The quality evaluation results provide a basis for decision-making, guiding whether the production process needs to be adjusted and optimized.
(7) Feedback and quality improvement
Quality evaluation and decision-making information timely feedback on the various stages of the CNC machining process.
This feedback mechanism allows the team to quickly address quality deviations, optimize production, and improve processing quality.
(8) Implementation of feedback quality control
By using continuous feedback, quality improvement, closed-loop control, and ongoing optimization of the CNC machining process.
Each feedback for the next stage supports data and experience, driving continuous improvement in the quality control system.
The structure framework of the CNC machining process quality control system is shown in Figure 2.
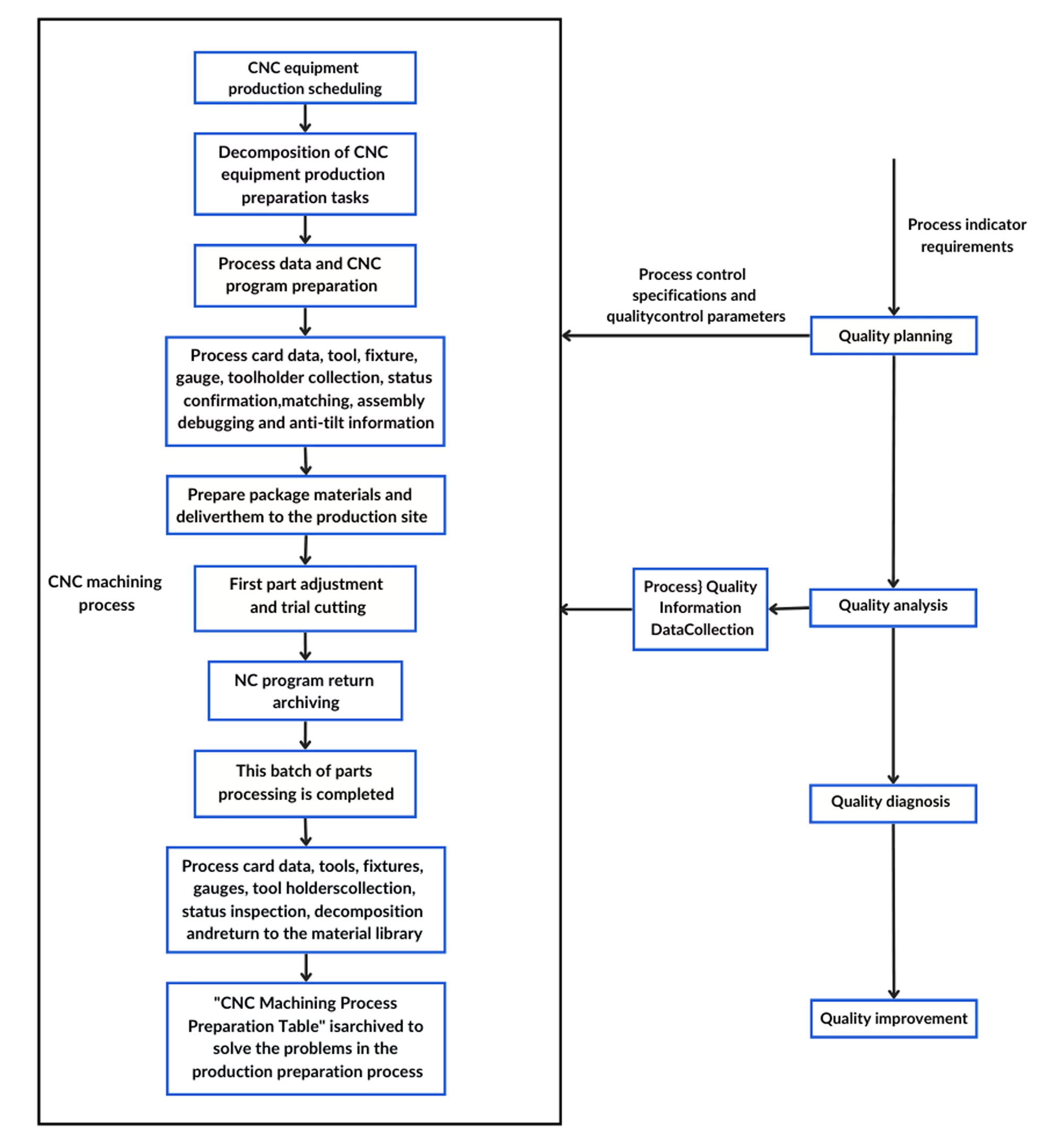
Figure 2 CNC machining process quality control system structure framework
CNC machining process quality control key links
CNC machining process quality control consists of five key steps: designing machining programs, programming CNC, simulating processes for checks, applying quality control methods, and building a skilled CNC team.
1. CNC machining process program design
CNC machining process design includes determining machining content, analyzing part drawings, selecting process routes, specifying process details, and choosing appropriate tools.
Compared with traditional general-purpose machine tool processing, CNC machining, in many ways, follows similar basic principles.
CNC machining features high automation, different control methods, and higher costs, resulting in process specificity, design rigor, and a strong focus on adaptability.
The rationality of the CNC machining program is reflected in three aspects: the specificity and adaptability of the process, the rigor of the design, and the optimization of the program.
The reasonable process program provides the basis for preparing the CNC program, which is a prerequisite for programming.
If the process program is not designed adequately, it can cause errors in the CNC machining process. If the process program design is not optimized, it can increase workload and waste efforts.
The quality of the CNC machining program directly determines the overall machining quality.
2. CNC Programming
CNC program is the result of CNC programming output, reflecting the specific realization of the CNC machining technology program. The following aspects reflect its accuracy.
Accuracy of the mathematical model processing of parts:
In CNC programming, it is necessary to ensure that the mathematical model of the part is processed accurately.
Programming should define the coordinate system, and set the tool point, safety plane, and CNC machine attributes accurately.
Reasonableness of process division and sequence arrangement:
The CNC machining process should follow a logical sequence with precise step divisions.
The tool geometry, route, and cutting parameters must be properly selected, and command letters should follow the CNC system’s syntax.
The selection of cutting parameters must consider the material, tool, machine, machining allowance, and other factors.
Tool running track safety:
The tool path must avoid overcutting, undercutting, collisions, and interference with the CNC table, parts, and fixtures.
Advanced CNC programming involves selecting the right processing methods based on CNC machining characteristics, optimizing the functions of CNC machines and systems, and improving equipment performance and program efficiency. Specifically:
CNC equipment program operation rate:
The time it takes for CNC equipment to run a program (PRT) and its equipment usage ratio (EUT) during a specific period.
Equipment Machining Performance:
The ratio of actual to desired machining efficiency within a defined period.
This metric can be calculated based on material removed, spindle cutting time, number of parts processed, or equipment use time.
Popular CNC software like UGNX, MASTER CAM, and CATIA offers strong technical support for programming.
This software can ensure the accuracy and sophistication of CNC programming. The goal is the same: efficient and accurate CNC machining, regardless of the programming tool used.
3. CNC machining process simulation checking
The simulation of the CNC machining process is one of the core technologies of virtual manufacturing. It mainly uses geometric and physical simulation to ensure the accuracy and safety of the machining process.
(1) Geometric simulation
VERICUT CNC simulation software primarily focuses on geometric checks, using advanced 3D displays and virtual reality to simulate machining and machine tool operations for highly realistic results. The main role of geometry simulation is:
Checking the correctness of the tool trajectory: Ensure that the tool’s movement path in the CNC program meets the design requirements and avoids machining errors.
Geometric interference collision checking of machine tool movement:
Simulation can detect collisions between the machine tool and parts or fixtures, preventing damage.
Geometric simulation is an important part of the accuracy and safety check of the CNC machining process. It can effectively avoid unnecessary losses and reduce the risk of the process.
(2) Physical Simulation
A more accurate simulation requires simulating the physical phenomena in the machining process.
Physical simulation focuses on the actual mechanical and thermal phenomena that occur in CNC machining. The following are some typical applications of physics simulation:
Milling Process Dynamics Simulation Optimization:
Advanced enterprises use SIM-CUT software from BUAA to simulate milling mechanics and optimize cutting parameters.
The simulation can help further analyze cutting force, vibration, and other physical phenomena to improve processing efficiency and accuracy.
Finite Element Analysis Simulation:
Some enterprises use finite element analysis-based simulation systems to study the CNC cutting of complex aircraft parts.
A finite element machining model simulates the physical process, including material properties, boundary conditions, tool trajectory load, and stress distribution.
This helps study part deformation, machining accuracy, and related issues to better control deformation in complex large-part machining.
4. Systematic application of quality control methods and tools technology
CNC machining quality control ensures results meet standards by minimizing process fluctuations.
This process includes quality planning, control standard development, process capability analysis, and the use of statistical methods.
The main steps of quality control
Quality Planning: Quality planning must first control process quality indicators and control points.
Process capability survey and analysis: Each machining process survey identifies factors affecting quality fluctuations and prepares process quality tables, control documents, and CNC process quality control.
Data collection and analysis: Collect real-time, accurate quality data, analyze it using quality control methods, assess the process quality, identify key factors, implement interventions, and ensure the process meets expected quality goals.
The process capability index is an important parameter for assessing whether the process meets the quality control requirements.
It calculates a process’s capability index to determine whether it can meet the actual quality control requirements. When calculating the process capability index, it must be ensured that the process is in a stable, controlled state.
The accuracy of sample inference depends on the sampling method, sample size, and inter-sample variation. The larger the sample, the higher the correctness of inference.
Quality control methods
Quality control methods for CNC machining processes include:
Statistical analysis methods: Questionnaires, stratification, cause-and-effect diagrams, permutation diagrams, histograms, correlation diagrams, control charts, and 7 other statistical methods.
Qualitative analysis methods: Seven types of reflective analysis methods: correlation diagram, affinity diagram, system diagram, matrix diagram, matrix data analysis, process decision-making procedure, and arrow diagram.
These methods analyze and control quality fluctuations, ensuring precise control of part machining quality.
CNC machining requires quality data and considers operator skills and quality control to ensure efficient, flexible methods for controlling part quality during the machining process.
Process quality control methods and tools, part of the 2008 ISO 9001 quality management principles, ensure the desired effect of CNC machining.
5. High-quality CNC technical personnel team establishment
Effective teamwork in CNC machining involves roles like production planners, programmers, tool pre-setters, operators, and inspectors.
Each staff member’s quality awareness, responsibility, and skill directly impact machining quality and efficiency.
Establishing a skilled CNC workforce is key to improving production management in the digital production environment.
Current personnel division of labor and challenges
CNC Programming: Currently, preparing CNC programs in most companies is mainly the responsibility of process technicians.
Process technicians prepare new protocols, solve technical problems, optimize existing protocols, and create CNC programs.
The heavy workload limits the process technician’s ability to optimize CNC programming and conduct in-depth research.
CNC tool preparation and pre-conditioning: Full-time CNC machine preparation workers handle CNC tool preparation and pre-conditioning.
The technical research ability of these workers is often limited by their individual skills, education, and physical condition, hindering overall improvement in CNC tool-cutting performance.
The need for a highly skilled and specialized workforce
With the continuous development of the production mode of advanced digital manufacturing plants, enterprises’ requirements for CNC technicians are increasing.
Building a skilled CNC technician team is crucial to improve machining efficiency and quality. A high-quality CNC technology team can:
Enhance the technical level of process technicians’ CNC programming skills through training and seminars, enabling them to optimize and innovate programming in their daily work.
Strengthen tool performance research h: Improve CNC operators’ technical research skills and promote continuous tool performance development.
Effectively manage the production process: Enhance CNC machining efficiency and quality stability through team collaboration and synergy.
Practical Application
Figure 3 shows the use of CATIA V5R18 software for designing the process of a hydraulic booster shell, including creating a digital machining model to determine the process plan and optimize the tool path.
The CNC machining process simulation check interface is shown in Figure 4.

Figure 3 CNC machining process program design of the shell
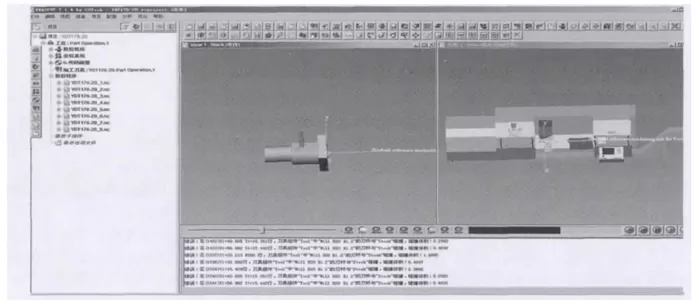
Figure 4 CNC machining process simulation check interface
CNC machining process simulation using VERICUT7.1 software showed that the process flow reduced from 195 to 21 procedures, and parts turnover decreased from 43 to 15 times after improvements.
Two cutting tools (Showa, single Deray) were used to optimize cutting parameters and determine efficient, practical processes.
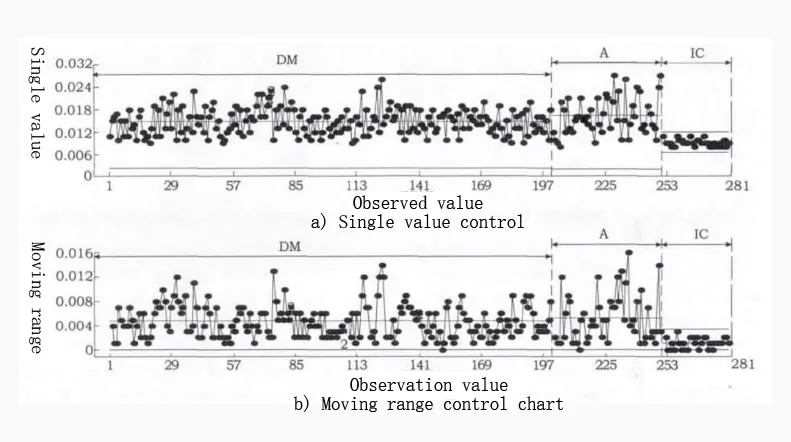
Figure 5 Single-value moving-pole control chart
The application of CNC machining process quality control to optimize production management and improve key tasks, such as bottleneck parts (shells), reduced the processing cycle from 4–5 months to just 24 days for four shell pieces.
The key measures to achieve results are as follows.
1) Develop a process improvement program by streamlining operations with the COBAR65 digital lathe, DMC60U vertical-horizontal machining centers, CNC drilling, and ROBOFORM2000 EDM machine tools as the core of four small units.
2) Production preparation is the basis for the success of this blitz. The special composite tool was pre-ordered for the technical improvement program, laying a solid foundation for process improvements. The production preparation team also played a key role in the part blitz process.
3) The new inspection method plays a key role. Process inspection tracks and records all parameters throughout the process, with general inspections conducted in advance, reducing total inspection time by half (only 2 days for a process that typically takes 4).
Conclusion
In CNC production transformation, the quality control model structure and key aspects must be verified through typical parts, using the “planning, analysis, diagnosis, and improvement” approach to assess the effectiveness and feasibility of efficiency improvement in similar manufacturing processes.