The global mold industry market will be around $285.5 billion in 2024. It has become a very large industry, and in this huge industry, the development of the materials used to manufacture molds and dies is also becoming more and more diversified.
The factors affecting the service life of the mold, in addition to the main design structure, forming and manufacturing process, heat treatment process and surface strengthening, lubrication and use of maintenance, and the selection of mold materials, have a great relationship.
According to the survey statistics, many factors cause mold failure, with improper mold materials and heat treatment accounting for about 70% of the failures. This shows that the correct mold materials and heat treatment to improve the mold life are important.
To let you understand this knowledge, we abandon the professional terminology, challenging to understand the charts, to simple and easy to understand the language to introduce.
First, the industry categorizes mold materials into cold work tool steel, hot work tool steel, and plastic mold steel.
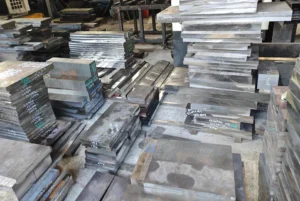
Cold work tool steel
Currently, commonly used cold work die steel includes CIMn low alloy tool steel, C2Mo, C2 high carbon, high chromium tool steel, and other materials.
CIMn steel has appropriate hardenability and wear resistance, and heat treatment distortion is small, but forging after the need to control the cold speed strictly makes it easy to form a reticulate carbide, resulting in the use of the mold in the chipping and cracking.
High-carbon, high-chromium tool steel has high wear resistance. Still, its carbide segregation becomes more serious, especially with large specification sizes, as the repeated upsetting and pulling effect is limited, causing deformation directionality and a decline in toughness.
Compared to C12Mo steel, D2 (Cr2MoV1) high-carbon, high-chromium tool steel slightly reduces carbide segregation, improves strength and toughness, and increases the mold’s service life to varying degrees.
High-speed steel offers higher wear resistance and strength and serves as a common material in mold making, but its toughness falls short of meeting the demands of complex, large, and shock-loaded molds.
Features include:
High hardness: after hardening treatment, cold work die steel can reach a high hardness level, usually around 60-65 HRC.
Good wear resistance: suitable for cutting and stamping work, etc., and able to maintain a long service life under high friction conditions.
High compressive strength: it can withstand greater pressure and is suitable for use in molds for heavy-duty work.
Toughness and crack resistance: Although the hardness is high, it maintains toughness to a certain extent and can withstand shock loads.
It specifically divides into the following types:
1. Low alloy cold work die steel
The main characteristics of low alloy cold work die steel are good workmanship, low quenching temperature, small heat treatment distortion, excellent strength and toughness, and appropriate wear resistance.
Adding chromium or manganese to the steel can improve the hardenability and make the steel in the quenching and low-temperature tempering to retain a certain amount of residual austenite, reduce distortion; adding silicon or nickel can enhance the matrix toughness, and improve the tempering resistance.
Adding molybdenum or vanadium can refine the grain in the same hardness and higher toughness than similar steels.
For example, GD steel (6CMnNMoVSi steel) heat-treated distortion is small, suitable for producing easy to chipping fracture of the cold stamping die, has a high service life.
DS steel is a high-toughness, impact-resistant cold work die steel mainly used for making impact-resistant shear, stamping, and punching molds; service life is significantly better than other high-toughness insert materials.
Application: suitable for producing cold punching die, impact resistant shear, punching, and punching molds, service life is significantly better than other high toughness insert materials.
2. Flame-hardened steel
Automotive production lines mainly use flame quenching steel for mold parts because of its wide range of quenching temperatures, good hardenability, strong toughness, and wear resistance.
or flame quenching, preheat the mold edge cutting surface to 180–200 ℃, then heat it to 900–1000 ℃ using a spray gun.
After quenching, the hardness can reach more than 60 HRC, forming a hardened layer of more than 1.5 mm. The distortion is generally only 0.02% to 0.05%.
The high-toughness matrix under the hardened layer provides strong support so that the edge of the mold is not easy to crack and chip and can significantly extend the life of the mold.
Application: Mainly used in mold parts of automobile production lines to extend mold life and reduce edge cracking and chipping.
3. Matrix steels
Matrix steels are a class of steels with the same chemical composition as the matrix in the quenched organization of HSS.
The carbon content of this type of steel is slightly higher than the matrix to increase the amount of primary carbide and improve wear resistance while adding a small amount of strong carbide-forming elements (such as niobium or titanium) to improve the process performance of steel.
Manufacturers widely use matrix steel in cold extrusion, thick plate cold punching, cold heading, and other molds. It is especially suitable for making large, complex molds and molds for difficult-to-deform materials.
Application: Widely used in cold extrusion, thick plate cold punching, cold heading, and other molds, suitable for making large and complex molds and molds of difficult-to-deform materials.
4. Higher toughness wear-resistant cold working die steel
To improve the C12 cold working die steel carbide segregation and further enhance the wear resistance of the steel, the relevant fields developed a variety of new steel, such as ID steel, ER5 steel, and GM steel.
These steels, through the appropriate reduction of chromium content, increase the content of tungsten, molybdenum, and vanadium to enhance the secondary hardening ability and wear resistance.
Compared with conventional C12-type cold work die steels, these have improved carbide segregation, toughness, and wear resistance. They are particularly suitable for high-speed punching machines and multi-station punching machine applications.
Application: Especially suitable for high-speed punching machines and multi-station punching machines.
5. Powder metallurgy high wear-resistant cold work die steel
The development of powder metallurgy technology and the application of hot isostatic pressing (HIP) have made producing and using powder metallurgy high-speed steel possible.
This steel has strong toughness, grindability, and isotropy; its heat treatment processability is better than the general high-speed steel, and it has a high service life.
Through the powder metallurgy process, it is also possible to produce high carbon, high vanadium, and high wear-resistant cold work die steel, which is difficult to manufacture by traditional methods.
Application: Suitable for producing high carbon, high vanadium, and high wear-resistant cold work die steel, the traditional method makes it difficult to manufacture special molds.
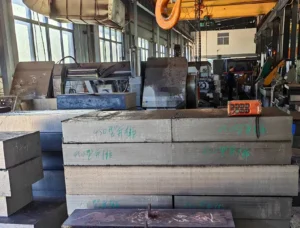
Hot work mold steel
Commonly used hot work die steel includes 5CMnMa5CNMo and 3C2W8V steel.
5CMmMo steel is used for small and medium-sized forging molds, and 5CNMo steel is mainly used for large and medium-sized ones.
However, the hardenability and tempering stability of 5CNMo steel is not high enough, and its performance cannot meet the demand of large cross-section forging molds.
3C2W8V steel is widely used in ferrous and non-ferrous hot extrusion and CAI alloy die-casting dies.
This steel has high thermal stability and can be used up to 650°C, but its thermal conductivity is low, and its cold and hot fatigue is poor.
H13 steel has good hot and cold fatigue, the use temperature does not exceed 600 ℃ can replace the 3C2W8V steel; mold life has been significantly improved, so H13 steel has quickly popularized.
To meet the new process of pressure processing and the latest equipment on the die steel in the toughness and thermal stability of the higher requirements.
1. Hot forging die steel
5CNMo steel is commonly used hot forging die steel, but its hardenability can not meet the large cross-section hammer forging die needs. When the cross-section size is greater than 300mm, the hardness of the heart makes it difficult to meet the requirements of a temperature that does not exceed 500 ℃.
5CNM steel is widely used for forging die steel, 55CNMoV6 is a German steel grade, these steels CNiMo contains a small amount of V can be hardened entirely in 400mm × 400mm cross-section, tempering stability is 100 ℃ higher than 5CNMo, used for a large cross-section of a hot forging die when the life of the die is higher than 5CNMo steel.
Compared with 5CÃNMoVSi steel, 5CÃNMoVSi steel has slightly lower carbon content, increased Cr and Mo content, and added the appropriate amount of V and Si to have high hardenability. After tempering, it is possible to maintain the same hardness on the surface and in the heart on a 500mm x 500mm section.
During tempering, the steel undergoes secondary hardening due to the precipitation of M2C and MC-type carbides. These improved steels offer significant advantages in high-temperature strength and toughness, and their service life is increased by a factor of 0.5 to 1.5 compared to previous steels.
Applications
– 5CNMo steel: Commonly used in hot forging dies, but for small cross-section dies, the applicable temperature does not exceed 500 ℃. It is more suitable for small cross-section hot forging molds.
– 5CNMoV6 steel: suitable for large cross-section hot forging dies (greater than 300mm), can be fully hardened in 400mm × 400mm cross-section, higher tempering stability, suitable for the higher requirements of hot forging molds, longer service life.
– 5CNMoVSi steel: high hardenability and significant high-temperature strength and toughness, service life is 1.5 times that of traditional steel, suitable for molds requiring high strength and toughness.
2. Hot extrusion die steel
H13 has been widely used in hot work die steel, in which the temperature does not exceed 600 ℃, and shows good hot and cold fatigue performance for hot extrusion die and aluminum alloy die casting die with high service life.
To improve its dimensional effect, some of the furnace refining, high-temperature diffusion annealing, isotropic forging process, and other methods such as electro slag remelting.
3C3Mo3V steel is a molybdenum hot work die steel with a performance between chromium and tungsten. By optimizing the ratio of alloying elements, many new hot works die steel in the high-temperature and hot and cold fatigue performance.
In recent years, new grades, such as QR080M and QR090M steels, have been developed that excel in resistance to high-temperature wear and overall performance.
Applications
– H13 steel: Widely used in hot extrusion dies and aluminum alloy die casting dies, suitable for use in environments with temperatures up to 600°C. It exhibits excellent hot and cold fatigue properties and has a long service life.
– 3C3Mo3V steel: suitable for hot work molds, performance between chromium and tungsten, with better high-temperature and hot and cold fatigue performance, suitable for molds used under high-temperature operating conditions.
– QR080M and QR090M steels: newly developed steels especially suitable for hot extrusion molds with high-temperature wear and comprehensive performance requirements, excellent high-temperature resistance and thorough performance.
3. Precipitation hardening steels
The characteristics of precipitation hardening hot work die steel is that the die is machined after quenching and low-temperature tempering. At this time, the hardness is about 40HRC and is used directly after machining.
The mold surface is due to heat carbide precipitation, resulting in secondary hardening, hardness up to 48HRC, while the heart maintains high toughness.
This steel does not have distortion and surface oxidation decarburization problems after heat treatment, so it is especially suitable for high-strength mold making.
Applications
– Suitable for high-strength molds, after quenching and low-temperature tempering, the hardness reaches 40HRC and can be used directly after machining.
The surface of the mold is due to heat carbide precipitation, the formation of the second hardening, and hardness up to 48HRC to maintain high toughness.
Plastic mold steel
Plastic molding with mold in the mold industry in the output value occupies an important position.
The performance of mold steel mainly has the following criteria based on plastic varieties.
These include comprehensive mechanical properties, good wear resistance, and excellent cutting performance.
Other criteria include polishing performance, pattern photo-etching performance, corrosion resistance, and welding performance.
The plastic mold frame and the technical performance requirements are not high for cavity molds.
Medium-carbon steels, such as S50C and S55C, are generally used.
This type of steel is in the normalized state with a hardness of 180–220 HB.
Due to the low hardness, poor resistance, and low surface finish, this type of steel made of mold life is low, and the quality of plastic products is poor.
You need to use special plastic mold steel for high technical performance requirements and long service life cavity mold.
In recent years, many new plastic molds have been developed with the progress of technology.
1. Pre-hardened plastic mold steel
Pre-hardened plastic mold steel is added to the base composition by adding appropriate amounts of Cr, Mn, Ni, Mo, V, and other elements.
Generally heat treatment is used to adjust the hardness to the requirements directly for mold manufacturing use.
Some typical steel chemical composition includes P20 steel, its quenching temperature of 830870 ℃, tempering temperature of 550600 ℃, and hardness of 30 ~ 35 HRC.
P20 steel is a widely used pre-hardened plastic mold steel suitable for making molds of different sizes.
Similar modified steel, such as 718 steel, has higher hardenability.
It also has uniform and consistent hardness after tempering, making it suitable for large cross-section mold manufacturing.
Application:
– P20 steel: widely used in producing plastic molds of different sizes, with moderate hardness and good processing performance.
Suitable for conventional plastic injection molds.
Hardness of 3035 HRC, tempering temperature 550600 ℃, suitable for standard mold manufacturing.
– 718 steel: with higher hardenability, suitable for making large cross-section plastic molds.
After tempering, the hardness is uniform and consistent, ensuring large molds’ strength and service life.
2. Free-cutting pre-hardened plastic mold steel
To improve the cutting performance of prehardened plastic mold steel, it can be added to the free-cutting elements.
These steels perform well in cutting performance.
However, the performance of large cross-section molds is somewhat limited by sulfides that increase anisotropy.
Calcium-treated steels improve the distribution of sulfides and alleviate this problem to some extent.
Applications:
– S series and SSe series steels have good cutting performance.
They are suitable for plastic molds requiring high machining accuracy.
However, large cross-section molds may be somewhat affected.
– 5NSCa steel: Composite easy-cutting technology optimizes cutting performance and anisotropy.
It is suitable for molds requiring high cutting efficiency and excellent machining performance.
3. Non-quenched plastic mold steel
Non-quenched plastic mold steel does not require tempering treatment.
It can reach the pre-hardened state through forging and rolling, shortening the production cycle and reducing costs.
For example, medium-carbon manganese boron air-cooled bainitic steel by adding SCa free-cutting elements to improve the cutting performance.
By controlling the chemical composition of the steel, uniform hardness can be achieved in large sections.
Application:
– Medium-carbon manganese-boron air-cooled bainitic steels improve cutting properties by adding a free-cutting element (e.g., SCa).
They are suitable for manufacturing plastic molds that require a pre-hardened condition with a short production cycle.
– Suitable for large cross-section molds, with uniform hardness and good machinability.
4. Age-hardening steel
Age-hardening steel is divided into martensitic aging steel and low-nickel aging steel.
Among them, low-nickel aging steel is more cost-effective.
This type of steel can achieve high hardness and comprehensive mechanical properties through an appropriate heat treatment process.
It is suitable for making high-precision and transparent plastic product molds.
Application:
–Martensitic and low nickel aging steel are suitable for making high-precision and transparent plastic product molds.
They offer high hardness and comprehensive mechanical properties.
Low nickel aging steel is cost-effective.
5. corrosion-resistant plastic mold steel
Plastic molds in the processing of chemical corrosion plastic need corrosion-resistant steel with corrosion resistance, such as 4C13, 9C18, and 17-4PH.
Stainless steel is a corrosion-resistant steel that can be used through the appropriate treatment to ensure corrosion resistance and good machinability.
For example, GS-083S and 168S are some typical corrosion-resistant plastic mold steels.
Applications:
– 4C13, 9C18, and 17-4PH steels: Suitable for machining molds for chemically corrosive plastics with good corrosion resistance, suitable for plastic molds used in chemical environments.
– GS-083S and 168S: Typical stainless steel corrosion-resistant plastic mold steel ensures corrosion resistance after treatment.
It also offers better cutting and machining performance, making it suitable for the requirements of corrosion-resistant molds.
6. Cold extrusion plastic mold steel
The cold extrusion molding method is used because of its high production efficiency, high precision molds, and good surface finish.
It is also widely used in complex cavity plastic mold manufacturing.
Applicable steel types include industrial pure iron, low carbon steel, etc..
These steels require low hardness and usually require carburizing treatment after cold extrusion molding to improve surface hardness and wear resistance.
Application:
– Industrial pure iron and low carbon steel:
Suitable for cold extrusion molding of plastic molds;
Cold extrusion molding usually needs to be carburized to improve the surface hardness and wear resistance after molding, which is ideal for complex cavity mold manufacturing.
Conclusion
In summary, developing the material field provides various performance optimization options, such as hardness, cutting performance, corrosion resistance, etc.
Selecting suitable plastic mold steel requires comprehensive consideration of the mold size, the working environment, processing requirements, cost, and expected service life.
In this regard, RuiYi has professional engineers who provide professional advice to maximize customer satisfaction.
What are the common types of model steel?
Examples include P20, H13, S7, and D2. These vary in properties like hardness, thermal resistance, and machinability, making them suitable for different applications.
What are the typical applications of model steel?
Model steel is used in injection molds, blow molds, die-casting molds, stamping dies, and extrusion dies.
What properties make model steel ideal for mold making?
- High toughness and wear resistance.
- Excellent machinability for precise detailing.
- Resistance to heat and thermal fatigue.
- Dimensional stability under stress.
How is model steel different from regular steel?
Model steel is specifically alloyed and heat-treated to enhance properties like toughness, hardness, and resistance to deformation, making it suitable for tooling applications.
What is pre-hardened model steel?
Pre-hardened steel comes with a specific hardness level suitable for mold making, eliminating the need for post-machining heat treatment. Examples include P20 and 718 steel.
How do you select the right model steel for a project?
Selection depends on factors such as mold type, production volume, material to be molded, required hardness, and thermal resistance.
What are common machining challenges with model steel?
Model steel can be tough to machine due to its hardness. Proper tooling, cutting speeds, and cooling systems are essential to achieve precise results.